Winning the War Against Equipment: Failure Effective Strategies Unveiled
Equipment failure is like the notorious villain of an industrial tale, lurking in the shadows, ready to disrupt your operations and impact productivity
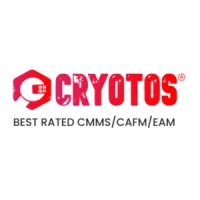
Equipment failure is like the notorious villain of an industrial tale, lurking in the shadows, ready to disrupt your operations and impact productivity