What Are Turn Key Turn Around Facilities?
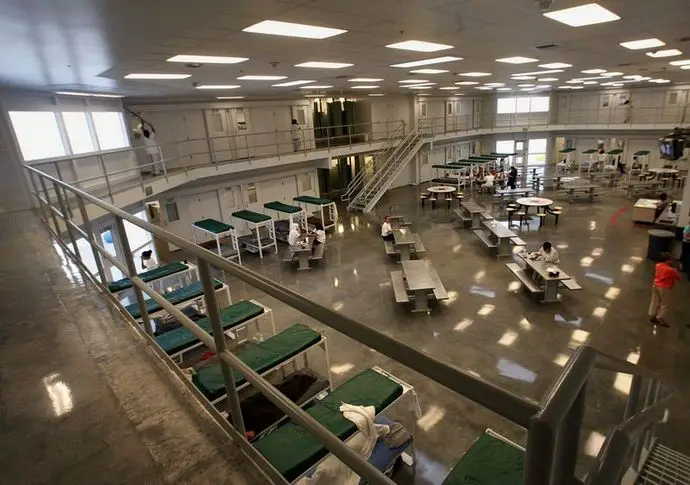
The Turn Key Turn Around Facilities refers to a product or service that is designed, supplied, built, or installed completely complete and ready to operate. The contractor or provider undertakes the entire responsibility for this process from design to completion and commissioning. Turnkey building solutions are the best way for clients to receive a fully functional home or business facility in a short amount of time. However, they can also pose a number of risks.
Cost
Turn Key turn Around Facilities are a great alternative for investors who don’t have the time or desire to purchase and manage properties on their own. However, investing in turnkey properties can be a risky proposition because they do not come with the benefit of knowing what the property will bring you in cash flow.
Often, turnkey companies will take care of all the details of the property, including financing, landscaping, cleaning, insurance, inspection and other costs associated with a new building. These fees can add up quickly and can cut into your bottom line.
Turnkey delivery strategies are gaining renewed attention as an effective means of managing complex facility needs for many institutions. Unlike traditional design-bid-build (DBB) and design-build (DB) approaches, turnkey solutions transfer risk, provide financial certainty and consolidate multiple aspects of development, construction and O&M into one comprehensive solution with financial and organizational flexibility.
Time
Turn Key Turn Around Facilities are a good example of a project that is ready for use upon completion. Unlike other projects where the owner has to pay for the project in full after its completion, with a turnkey project, the owner can purchase the building and start using it straight away.
A turnkey project involves a contractor or firm sourcing and purchasing supplies, designing and building the facility, and delivering it to the owner. This is usually a much faster process than having the owner perform these tasks.
It’s important to have a sourcing partner that has a strong track record of delivering efficient supply chain solutions. They should also be nimble enough to respond quickly to sudden market changes or new materials requirements.
Risk
Turn around maintenance shutdowns are necessary to inspect and maintain equipment – usually every four years or so. However, when they are not done well or a turnaround is extended too long, they can lead to fuel shortages, price increases and other issues.
The risk associated with turnarounds can be reduced through a number of different approaches. First, the risks are identified and assessed. Next, the total risk is compared with risk reduction measures which will reduce this risk.
Then the optimum level of expenditure Q towards risk reduction and total risk of failure K is achieved at which the total cost G = Q + K is minimized. This requires an iterative process which is the basis for integrated risk management. Risks are interrelated and are often ranked in order of magnitude. This approach is called Pareto analysis. It ensures that risk reduction efforts are targeted to those failure scenarios accountable for the majority of total risk.
Reliability
The reliability of a Turn Key Turn Around Facilities system is a topic of debate. For one thing, there are plenty of shady operators out there, but there are also many reputable and able-bodied firms that provide the services in question. Having a robust, well-run turnkey system in place can save a significant amount of time and money down the road by helping to keep your systems running smoothly and efficiently.
This can result in better outcomes for both you and your customers, a win-win situation in most cases. The best part is that the systems are typically maintenance free, allowing your staff to focus on other important tasks like delivering customer service and driving down costs. The key to success is implementing a sound system design and maintenance plan that can be adapted to suit your business’s changing needs.