What are the Socket Welded Pipe Fittings?
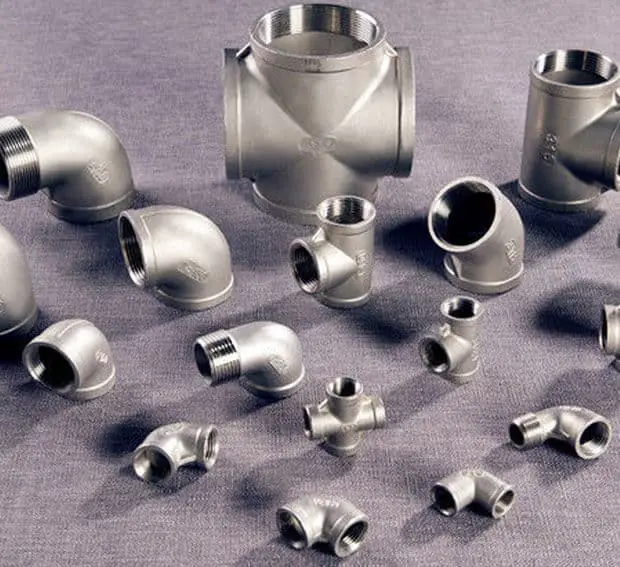
What are Socket Welded Pipe Fittings?
Installing Socket Welded Pipe Fittings requires some skill and knowledge of basic welding principles. First, all surfaces must be cleaned before fitting begins – this will ensure that no contaminants or foreign objects enter the joint during installation. Once everything has been cleaned off, one end should be heated with a torch until it reaches its melting point (usually around 700 degrees Celsius). Then, both ends should be brought together quickly while being held in place with a wrench – this helps ensure that no air bubbles form between them during welding. Finally, once both ends have cooled down, they should be inspected to ensure there are no leaks or other issues in the joint before they can be used safely in your application.
Socket welding pipe fittings consist of four main parts:
- The body.
- The end connection or hub.
- The circular gap between the two pieces (called a socket).
- The fillet radius.
The body is typically made from stainless steel and is designed to fit over the hub of another fitting or pipe. The hubs can be threaded or plain-end, depending on what type of connection you need. When two pieces are joined, the socket provides an air-tight seal using heat fusion welding. Lastly, the fillet radius provides additional strength and stability for the joint by ensuring adequate material at all points where stress is applied.
Applications of Socket Welded Pipe Fittings
Socket weld pipe fittings are typically used in applications where tight seals are required – such as water systems, gas lines, and oil rigs – because they provide an air-tight seal when connected properly. They can also be used in high-pressure applications since their fillet radius helps increase their stability under load. Lastly, socket welded pipe fittings offer an easier installation than other types due to their simple design, which only requires heat fusion welding to join pipes securely.