What are the Benefits of Using a Spray Dryer for Powder Production?
Spray drying is a highly efficient method of producing dry powders from liquid materials, with benefits including uniform particles, improved solubility, and reduced processing time and cost. When choosing a spray dryer supplier, factors to consider include material type, particle size, and operating efficiency.
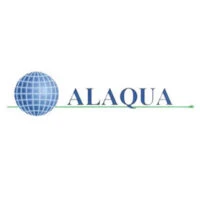