What are the Advantages of Fine Blanking?
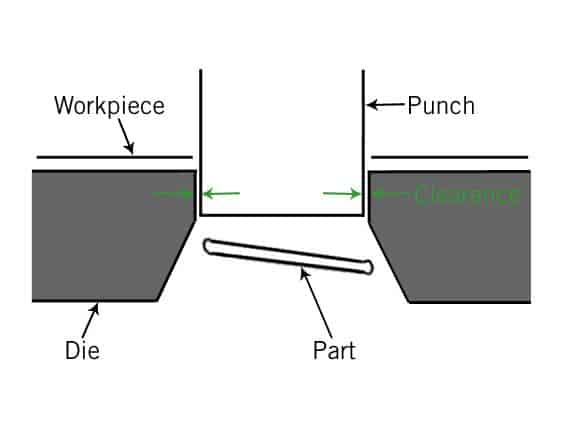
What is fine blanking in manufacturing?
Fine blanking(also known as fine-edge blanking) is a special type of stamping process that produces parts of enhanced accuracy, flatness, and edge characteristics when compared with conventional stamping.
Fine blanking may be used to manufacture bevels, multiple, and complex gear sets which are difficult to produce by stamping. Gears made by fine blanking possess excellent dimensional accuracy and surface finish and have comparatively higher strength than those made by stamping and powder metallurgy.
Moreover, fine-blanked gears have widespread applications including automotive, office equipment, appliances, medical equipment, electronic instruments, etc., displays a variety of gears manufactured by this type of blanking.
Let’s talk about its advantages in detail and that will give you more idea about this kind of blanking.
The Advantages of Fine Blanking in Manufacturing
- It creates a precise and finished surface
Fine blanking enables the production of high-precision parts by non-cutting and, if desired, simultaneous forming.
The punch moves from bottom to top during blanking. The raw material is held along the cutting contour by means of a so-called ring jig.Only then does a stamp with the desired shape cut the metal.
In combination with a considerably reduced cutting gap, a cylindrical cutting portion of up to 100 % of the sheet thickness with exactly right-angled cutting edges is achieved, but with thin sheets the cutting gap becomes very small.
- Optimum speed that achieve 100 strokes per minute and more
In this kind of blanking, the work-piece is pushed back into the mould via an ejector, before being ejected via the so-called counter-holder force and finally blown out or removed.
Whereas in the past only around 40 to 50 strokes per minute could be achieved with this blanking, modern presses today achieve strokes of up to 100 strokes per minute and more.
In addition to all this, the servo drive with the corresponding control system made it possible to finally eliminate the cutting impact.
Speed parameter
Due to the servo-controlled hydraulic drive, the precisely controlled speed within each individual power stroke can be adapted to each process. A rapid traverse stroke shortens the cycle time, as does a shorter opening stroke when thin parts are to be cut.
- Minimizes plastic deformation
Fine blanking makes use of additional supporting tools (pads) and impingement technology to minimize plastic deformation during the shearing process.
Fine-blanked gears are used in automotive parts, appliances, office, and medical equipment.
- Has an edge over conventional blanking
Precision fine blanking is a specialized manufacturing process that produces parts with extremely tight tolerances and a clean edge, free of die breaks and tears on most materials, enhancing the aesthetic value of the part.
The material’s precision cut edge is meticulously produced through a finely tuned metal stamping process that cannot be produced through conventional means.
Summary
Let’s conclude it!
Fine blanking is similar to extrusion where the metal is extruded through die cavities to form the desired gear tooth geometry. It is also similar to stamping but differs in the sense that it uses two opposing dies to form the gear from sheet material.
And now, when you’re aware of its benefits over other kinds of blanking, you will understand the reason behind its popularity.
0