The Ultimate Polyolefin Plastomer (POP) Production Process Report
Polyolefin Plastomers (POPs) represent a unique class of polymers derived from the polymerization of olefins.
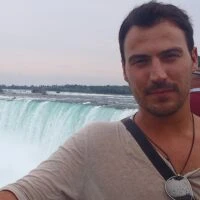
Polyolefin Plastomers (POPs) represent a unique class of polymers derived from the polymerization of olefins.