The Guide to Choosing the Right Hazardous Area Cables?
In the realm of industrial operations, ensuring safety and reliability is paramount. One critical aspect that demands meticulous attention is the selection of appropriate hazardous area cables. These specialised cables play a pivotal role in hazardous environments where the presence of flammable gases, vapours,
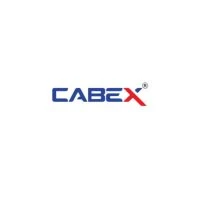