The Basics of Semiconductor Dicing
Semiconductor dicing is a process used in the manufacture of electronic components. It is used to separate ...
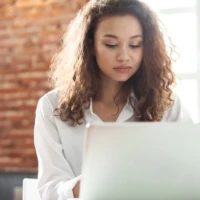
Semiconductor dicing is a process used in the manufacture of electronic components. It is used to separate ...