"The Art of Brazing: A Versatile Metal-Joining Technique"
In the world of mechanical engineering, joining materials is a fundamental aspect that drives innovation and functionality across various industries. Among the many ...
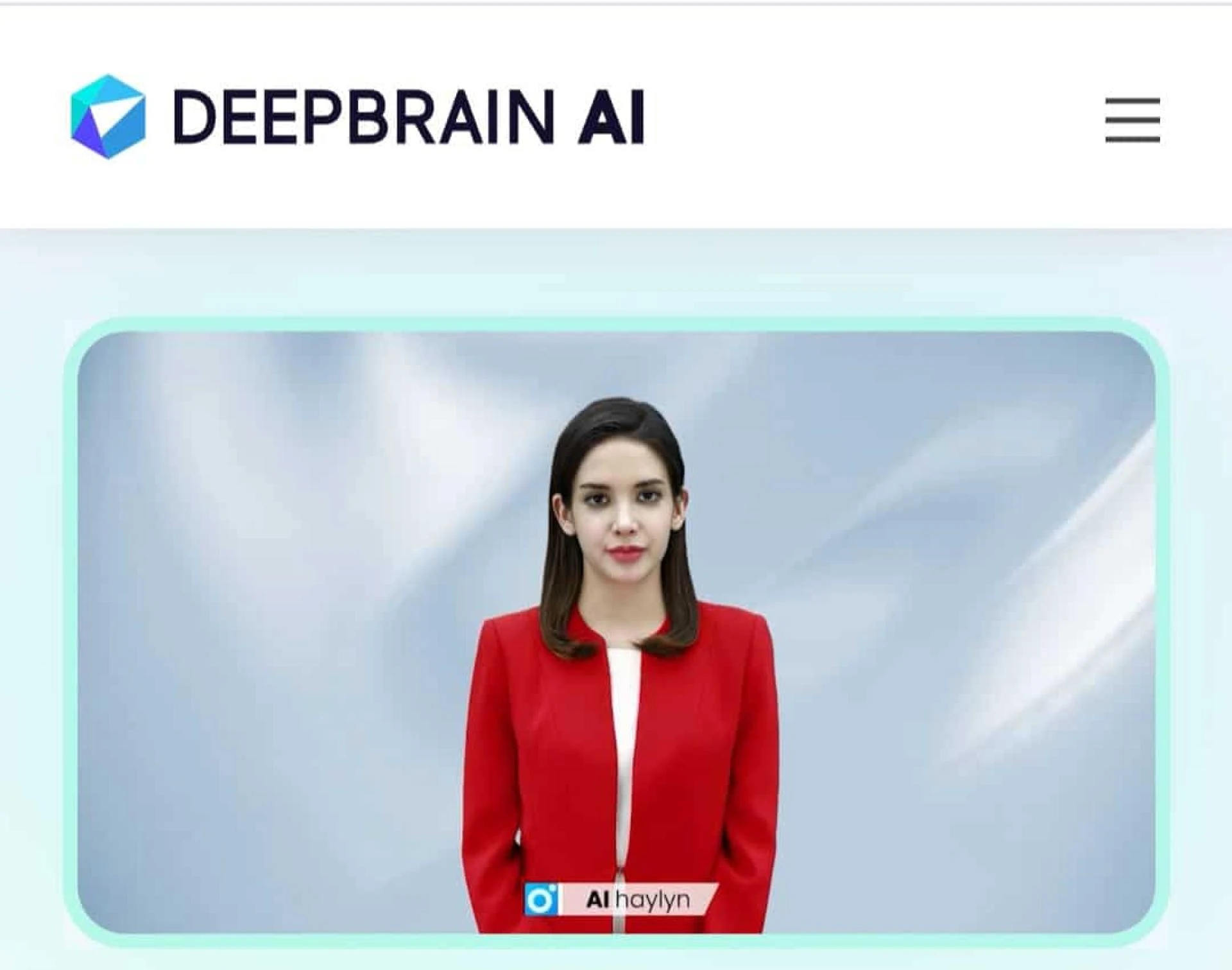
In the world of mechanical engineering, joining materials is a fundamental aspect that drives innovation and functionality across various industries. Among the many ...