Process of Manufacture Pharmaceutical Ointments
An efficient technique to deliver active chemicals to the affected body area is through a cream or ointment. It treats pain, burns, itchiness, ...
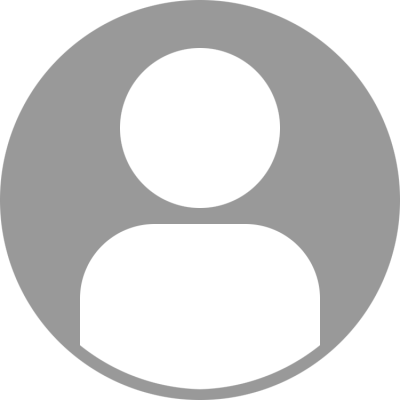
An efficient technique to deliver active chemicals to the affected body area is through a cream or ointment. It treats pain, burns, itchiness, ...