Mastering Serigraphy: Techniques and Tips for Stunning Prints
Introduction to SerigraphySerigraphy is a stencil-based printing method that involves transferring ink through a fine mesh screen ...
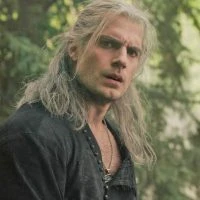
Introduction to SerigraphySerigraphy is a stencil-based printing method that involves transferring ink through a fine mesh screen ...