Key Factors to Consider When Designing with Epoxy Insulators
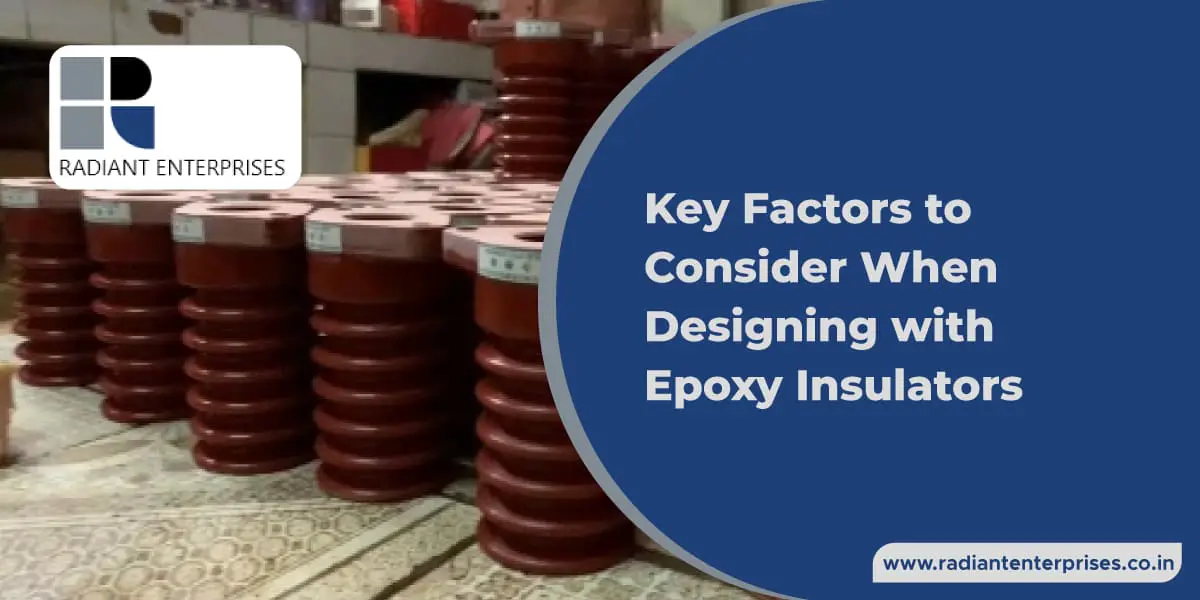
Epoxy insulators are essential in the field of electrical engineering, where they guarantee the security and dependability of several electrical equipment and systems. Epoxy resin is used to create these insulators, which are superior in electrical, mechanical, and thermal qualities. If you want your power transformers, circuit breakers, and switchgear to function at their best and last as long as possible, you need to know what to look for in an epoxy insulator. This blog will discuss the key considerations that engineers need to keep in mind throughout the design phase in order to get the most out of epoxy insulators.
Material Selection:
The foundation of a successful design is the careful selection of the appropriate epoxy substance. Epoxy can be formulated in a variety of ways, each of which results in qualities that are tailored to a particular use. When choosing epoxy insulators, it is important to take into account a number of different characteristics, including dielectric strength, thermal conductivity, the coefficient of thermal expansion, and flame resistance. To select the most appropriate material, it will be helpful to have a comprehensive grasp of the operating environment, the voltage levels, and the temperature range.
Electrical Properties:
Epoxy insulators are required to keep their electrical integrity despite changes in the electrical loads applied to them and the circumstances of their environments. It is of the utmost importance to evaluate the insulator in terms of its dielectric strength, breakdown voltage, and insulation resistance. In addition, you need to think about the effects that humidity, temperature variations, and pollutants have on the performance of the electrical system. If these elements are properly analysed, then the insulator should be able to withstand the electrical forces that it will be subjected to.
Mechanical Design:
Epoxy insulators’ performance and dependability are directly influenced by the mechanical design of the insulating material. Think about the mechanical strains that will be put on the insulators throughout the installation, operation, and maintenance of the system. In order to avoid mechanical failure or cracks in the epoxy, it is vital to have characteristics such as mechanical strength and stiffness, as well as resistance to vibrations. A correct mechanical design should also take into account the distribution of stress in order to avoid points of concentration.
Thermal Considerations:
Temperature shifts are not uncommon in the context of electrical applications. Insulators made of epoxy should be built to withstand the wide range of temperatures that can occur while the material is in use. Conduct an analysis of the coefficient of thermal expansion to determine how best to reduce the amount of strain placed on the epoxy by changes in temperature. In addition, thermal conductivity is an important factor to take into account in order to guarantee effective heat dissipation and avoid the formation of localised hotspots that could cause the epoxy material to deteriorate. Expand your business frontiers with the exports of Epoxy insulator in Germany and embrace international success!
Environmental Compatibility:
Insulators made of epoxy may be subjected to difficult environmental conditions, including contact with water and chemicals, as well as ultraviolet light. Epoxy materials that are resistant to these factors are the only option available to engineers who want to prevent epoxy from degrading over time. To assure the insulators’ dependability in the field, you should run exhaustive tests to evaluate their functioning over the long term in a variety of different environmental situations.
Creepage and Clearance Distances:
In high-voltage applications, variables like creepage and clearance distances are of the utmost importance. Arcing and tracking between conductive parts are both avoided thanks to this spacing. To ensure that there is sufficient electrical isolation on the surface of the epoxy insulator, it is necessary to accurately calculate and design the creepage and clearance distances.
Manufacturing Process:
Epoxy insulators can experience substantial shifts in both their quality and uniformity depending on the production process. Check to see that the technique of manufacturing you’ve chosen is able to produce the correct shapes and dimensions with the required level of precision. During production, it is vital to implement stringent quality control methods in order to eliminate flaws and maintain uniformity throughout the batch.
Testing and Certification:
Conduct exhaustive tests on epoxy insulators to validate whether or not they meet the requirements outlined in industry standards. Obtain certificates from the appropriate regulatory agencies to confirm that the insulators satisfy the necessary standards for both safety and performance. Certifications lend legitimacy to your electrical equipment business and instil confidence in customers who are considering purchasing it.
Final Thoughts:
When designing with epoxy insulators, it is necessary to take a holistic approach, taking into account many elements such as the selection of the material, the electrical properties, the mechanical design, the thermal considerations, the environmental compatibility, the creepage, the clearance distances, the manufacturing process, testing, and certification. The overall performance, dependability, and safety of electrical equipment are all improved by each of these aspects individually. Engineers are able to tap into the full potential of epoxy insulators and construct durable electrical systems that are capable of keeping up with the demands of modern technology if they give careful consideration to the important elements listed above. Step into the Italian market and get involved in the Exports activity of Epoxy Insulator in Italy and make your mark in Europe!