Inventory Reduction Requires Adequate Planning
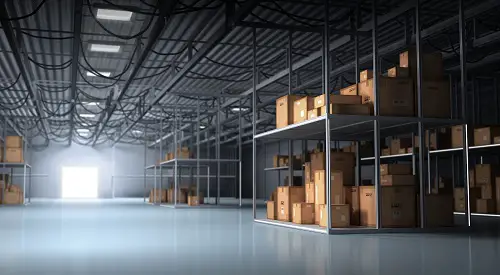
An effective and efficient inventory reduction technique goes a long way in both the success and failure of an organization. A severe reduction in available inventory lead time will inevitably result to goods / raw materials not being held in storage for a sufficiently long period of time. Both a severe reduction in manufacturing and supplier lead time will also contribute to inventory reduction, with corresponding effects on profit margins. There are also a potential impact on pricing, as well as on the ability to absorb costs related to excess inventory. To conclude that inventory is always decreasing is to state the obvious – but this can only partly be true in a world where a large number of organizations have adopted the “green” methods of managing their inventory.
When considering inventory reduction, it is often assumed that the source of shortfalls is a poor quality product or a lack of marketing. There are other reasons which are more difficult to determine, but in order to manage inventory reduction effectively, it is important to conduct regular safety stock review for every department, regardless of its activity level. A regular schedule of inspections should be designed and strictly adhered to. In addition to having a regular inventory inspection schedule, it is important to identify and address the risks that could affect the process of reducing the available inventory. These include issues such as the ability of the business to store the products safely, the nature of the products themselves, whether the products pose any threat of harm to the environment, and other considerations relevant to the operations of the business.
Many companies underestimate the amount of waste that occurs during the supply chain process, particularly in terms of product returns and the time taken to improve the supply chain process. Although the overall goal of supply chain improvement is to improve the reliability of the entire process, managers and supervisors often overlook the issues which are specifically related to their department. By regularly auditing the supply chain process, inspectors can spot problems that may impact the process and the efficiency of the overall operations. Audits should be conducted not only on a department-by-department basis but also by integrating all areas of the supply chain, such as manufacturers, distributors, wholesalers, and suppliers.
Another key component of effective inventory reduction is planning. The plans and strategies developed by the various departments should be reviewed periodically in order to identify any changes or missed opportunities to reduce excess inventories. The strategies must be developed according to the existing demand, the existing stocks, and the current process and operational parameters. In addition to developing appropriate plans, a manager should also develop the staff to execute the strategies and plans. The effectiveness of the plans and strategies largely depends on the people assigned to execute them. Employees must be properly trained, and supervision of employees must be consistent and reliable.
Implementing an ERP system and integrating it with supply chain management can significantly reduce the operational cost of an organization. Implementing an ERP system requires a significant investment from the company, but the benefits far outweigh the costs. Implementing an ERP system and integrating it with supply chain management offers numerous advantages, including increased productivity, increased profitability, better quality control, simplified reporting, and increased control and accuracy.
Inventory planners are critical to the management of any supply chain or ERP system. The planners provide critical and timely information needed to guide inventory reduction, planning, and dispatch. There are three key roles that a quality inventory planner plays. First, the planner provides critical information necessary to support the planning, management, and dispersion. Second, the planner minimizes the potential for errors in the dispersion and planning by training workers to perform their tasks in a reliable, organized, and error-free manner. Lastly, the planner and his or her team effectively manage and control toxic materials by identifying the most suitable routes for moving them in accordance with their specific requirements and conditions.