Important Things to Know About a Custom Enclosure Manufacturer
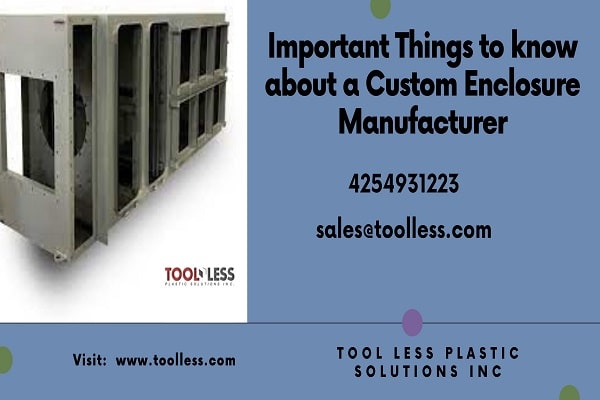
Plastic enclosures are suitable to accommodate and secure sensitive electronic and electrical parts. Nowadays, a majority of manufacturers develop plastic housings from flame-retardant ABS and impact-resistant polycarbonate.
Plastic enclosures are ideal for indoor and outdoor applications. Available in a wide variety of sizes and shapes, plastic enclosures guarantee the safety and durability of the components.
The main reason behind the popularity of plastic enclosures is their ability to safeguard electronic components from external factors.
Note that the applications of plastic enclosures are limitless. From industrial control boxes to wireless and telecommunication boxes, plastic enclosures are omnipresent. Here are some important things to know about plastic enclosures.
Type of Plastic used by the Manufacturer in Plastic Enclosures
Usually, there are a handful of plastics that the manufacturers can use to develop plastic enclosures. Here are some of the types of plastics commonly used by manufacturers to create plastic enclosures.
ABS Plastic
Acrylonitrile Butadiene Styrene, also known as ABS, is one of the toughest thermoplastic polymers. Nowadays, it is common among manufacturers to use ABS for developing high-quality plastic enclosures.
Even when exposed to extreme atmospheric conditions, ABS can provide proper protection to the sensitive components. Manufacturers count on its durability to create high-quality and sturdy plastic enclosures.
Polycarbonate (PC)
Polycarbonate belongs to the polyester family. It is a highly popular thermoplastic because of its strength and flexibility. Nowadays, polycarbonate has vast applications in various industry domains. From eyewear to medical devices, you’ll find polycarbonate everywhere.
Polycarbonate is highly transparent and easily colorable. That’s why a custom enclosure manufacturer relies on polycarbonate to manufacture plastic enclosures.
Another key attribute of polycarbonate is that it resists UV rays. As a result, polycarbonate is rapidly emerging as the go-to material to manufacture plastic enclosures. Furthermore, because of its flexibility, polycarbonate is ideal for creating custom plastic enclosures.
Polyamide (PA)
Polyamides occur naturally in the form of proteins. Therefore, polyamides are an integral component of cable ties and power tool housings.
One of the key highlights of polyamides is that they are tear-resistant. Usually, manufacturers use polyamides to create plastic enclosures for indoor applications only. It is also a great electrical insulator. However, it is not water-resistant, which can be an issue.
Ratings of the Plastic Enclosures
You will find plastic enclosures with various types of letters and numbers printed on them. These letters and numbers are actually ratings provided by international organizations. As a consumer, you should always be aware of these ratings.
IP Rating
Also known as the Ingress Protection marking, IP rating refers to the resistance of a plastic enclosure against dust and water. The IP rating usually contains numbers and letters. For example, if the first digit of the IP rating is 6, it implies that the plastic enclosure is dustproof.
UL Rating
UL is the acronym for Underwriters Laboratories. UL rating implies the fire resistance capabilities of a plastic enclosure. Any good plastic enclosure should have a UL rating of 94VO.
If you want custom plastic enclosures, opt for the services of Toolless. They can manufacture a wide variety of highly customized plastic products.