How to Minimise the Peril Factors of Stress Corrosion Cracking
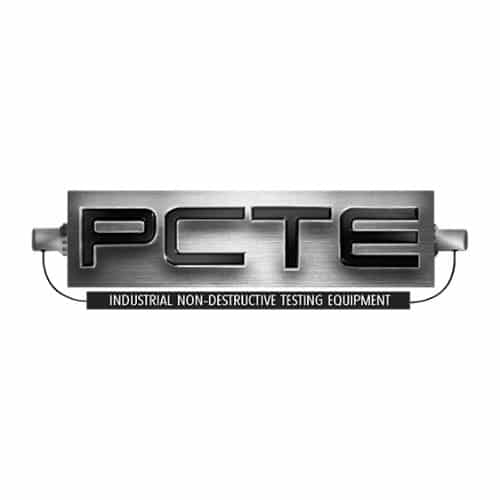
Stress corrosion cracking is a galvanic corrosion caused by the combined effect of tensile stress and corrosive environmental conditions. Detection of such corrosion’s is possible well before it destroys the whole structure. Hence, it is repairable before it goes beyond restoration, or before the cost to restore breaks your bank.
Causes of Stress Corrosion Cracking
There are three main reasons due to which this cracking happens.
- Applied stress
- Increased temperature
- Susceptible materials like chlorides and hydrogen sulphide
All these factors are required for the corrosion to occur. However, the conditions may vary depending on the material in question.
Minimizing the Peril Factors
Many companies plan and keep a regular check on the material to ensure it is not affected by stress corrosion cracking. The examinations are a regular thing so that defects (if any) can be detected well on time, as it is sometimes not visible with the naked eye. Other things that you can do to minimise their peril factors are:
Suitable Material
In many cases, stress cracking is avoidable by using a better quality suitable material. Also, avoid any tensile stress concentration occurring on the edges. Using better material, keeping in mind the environmental conditions and other factors, can save you from a lot of trouble.
Temperature
Studies show that cracking can occur at a temperature of around 60 degrees Celsius. However, the situation gets worst above 80 degrees Celsius. You can minimise the effects by controlling operating temperatures as well as the electrochemical potential of the alloy.
Cracking Type
Be aware of the cracking or corrosion that your metal or alloy is prone to. Two types are namely: chloride-induced and H2S induced. For chloride-induced cracking, it is advisable to use metals like stainless steel with considerably high nickel content. Whereas concerning the H2S induced cracking, high nickel content works well for almost all environmental conditions.
Understand that it is during the design phase that you can manage the avoidance. Also, you must have an expert team by your side to help you find the best solutions to minimise the risks to the metal that stress corrosion cracking can cause.
About the author
PCTE Industrial is a specialist in the sale and hire of industrial non-destructive testing (NDT) equipment. PCTE INDT is a branch of PCTE, who has been serving in the NDT industry since 2008. We offer a range of INDT equipment that covers the bread and butter applications but also adds some exciting technology. Our range covers devices for Ultrasonic Testing (UT), Eddy Current (ET), Magnetic Particle (MT), Dye Penetrant (DT) and Visual Testing (VT).