How to Maximise the Benefits of PVDF Raw Material ?
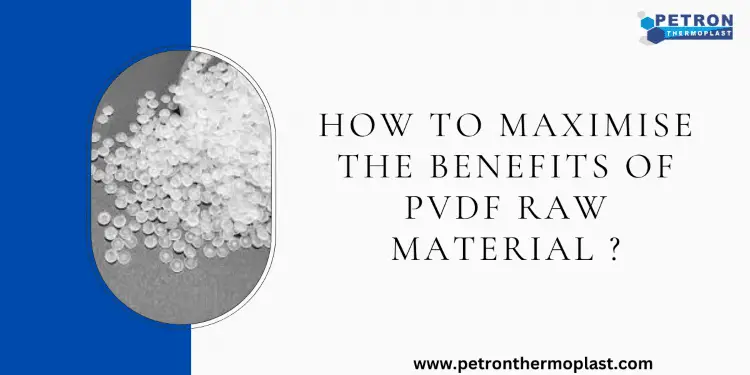
Introduction
Polyvinylidene fluoride (PVDF) is a versatile polymer known for its remarkable properties and wide-ranging applications across various industries. As a raw material, PVDF offers exceptional chemical resistance, thermal stability, mechanical strength, and UV resistance, making it highly desirable for diverse applications. In this guide, we delve into strategies to maximise the benefits of PVDF Raw Material, exploring its uses, processing techniques, and potential challenges.
Understanding PVDF Raw Material
PVDF, a semi-crystalline thermoplastic fluoropolymer, is derived from the polymerization of vinylidene fluoride monomers. Its unique molecular structure contributes to its outstanding properties, including high purity, excellent chemical inertness, and resistance to harsh environments. PVDF Raw Material exists in various forms, including pellets, powders, and solutions, offering flexibility in processing and application.
Key Properties
- Chemical Resistance: PVDF exhibits exceptional resistance to acids, bases, solvents, and harsh chemicals, making it ideal for applications in chemical processing, semiconductor manufacturing, and oil and gas industries.
- Thermal Stability: With a high melting point and heat resistance, PVDF maintains its integrity and mechanical properties across a wide temperature range, from cryogenic temperatures to elevated temperatures, ensuring reliability in extreme conditions.
- Mechanical Strength: PVDF Raw Material boasts high tensile strength, toughness, and abrasion resistance, making it suitable for demanding structural applications, such as piping systems, automotive components, and architectural elements.
- UV Resistance: The inherent UV stability of PVDF makes it suitable for outdoor applications, including cladding, roofing, and signage, where long-term exposure to sunlight is inevitable.
Applications of PVDF Raw Material
PVDF Material finds extensive applications across diverse industries, owing to its unique combination of properties:
- Architectural Coatings: PVDF-based coatings offer durable protection and vibrant colours for architectural facades, window frames, and metal roofing, enhancing aesthetics and longevity.
- Chemical Processing Equipment: PVDF’s chemical resistance and thermal stability make it ideal for manufacturing chemical storage tanks, pipes, valves, and fittings, ensuring safety and reliability in corrosive environments.
- Electrical Insulation: PVDF films and coatings serve as excellent electrical insulators in electronic components, cables, and wires, providing high dielectric strength and reliability in demanding electrical applications.
- Membrane Filtration: PVDF membranes play a crucial role in water treatment processes, facilitating efficient filtration and separation of contaminants in municipal and industrial wastewater treatment plants.
- Medical Devices: PVDF is utilized in medical applications, such as catheters, implants, and surgical instruments, due to its biocompatibility, sterilizability, and resistance to bodily fluids.
- Photovoltaic Films: PVDF films are employed as encapsulation materials in solar panels, offering protection against moisture, UV radiation, and mechanical stress, thus enhancing the durability and performance of photovoltaic modules.
Processing Techniques
Optimal processing of PVDF Raw Material is essential to harness its full potential and achieve desired properties in finished products. Several processing techniques are employed:
- Extrusion: PVDF pellets are melted and extruded through a die to form pipes, sheets, profiles, and films. Controlling melt temperature, screw speed, and die design is crucial to prevent degradation and achieve uniformity in extruded products.
- Injection Moulding: Molten PVDF is injected into a mould cavity under high pressure and cooled to form intricate shapes, such as valves, fittings, and components for automotive and aerospace applications. Proper mould design and temperature control are critical to avoid warping and defects in moulded parts.
- Compression Moulding: PVDF powder is placed in a mould cavity and compressed under heat and pressure to form solid shapes with precise dimensions and surface finish. Optimising moulding parameters, such as temperature, pressure, and cycle time, ensures consistency and quality in compression-moulded products.
- Coating and Lamination: PVDF coatings are applied onto substrates through techniques like spray coating, dip coating, or powder coating, followed by curing to form a durable, protective layer. Lamination involves bonding PVDF films to substrates using adhesive or heat, imparting desired properties, such as barrier protection and weather resistance.
- Solution Casting: PVDF solutions are cast onto a substrate and dried to form thin films or membranes with controlled thickness and properties. Solvent selection, drying conditions, and post-treatment processes influence the morphology and performance of solution-cast PVDF films.
Challenges and Solutions in Working with PVDF Raw Material
While PVDF offers exceptional properties, certain challenges may arise during processing and application. Addressing these challenges is crucial to ensure optimal performance and product quality:
- High Processing Temperature: PVDF has a relatively high melting point, requiring elevated processing temperatures that may lead to thermal degradation and discoloration. Employing efficient heat transfer mechanisms, such as hot air or infrared radiation, minimises thermal degradation and enhances process stability.
- Poor Adhesion: Due to its low surface energy, PVDF may exhibit poor adhesion to substrates, affecting coating adhesion and bonding in laminated structures. Surface treatment techniques, such as corona treatment or plasma activation, improve substrate wettability and adhesion of PVDF coatings and films.
- Crystallinity Control: The crystalline structure of PVDF influences its mechanical properties, chemical resistance, and processability. Controlling processing parameters, such as cooling rate and annealing conditions, enables precise manipulation of PVDF crystallinity and morphology to meet specific application requirements.
- Environmental Stress Cracking: Exposure to certain chemicals and environmental factors may induce stress cracking in PVDF components, compromising their integrity and performance. Selecting appropriate PVDF grades with enhanced chemical resistance and designing components to minimise stress concentrations mitigate the risk of environmental stress cracking.
Conclusion
Maximising the benefits of PVDF Raw Material requires a comprehensive understanding of its properties, processing techniques, and potential challenges. By leveraging its exceptional properties and employing effective processing strategies, manufacturers can develop innovative solutions across diverse industries, enhancing performance, durability, and sustainability in various applications. With continuous advancements in materials science and manufacturing technologies, PVDF remains at the forefront of innovation, driving progress and meeting the evolving needs of modern industries.
Frequently Asked Questions (FAQ’s)
- What is PVDF raw material used for?
PVDF material is utilised in various industries for applications requiring chemical resistance, thermal stability, mechanical strength, and UV resistance. Common applications include architectural coatings, chemical processing equipment, electrical insulation, membrane filtration, medical devices, and photovoltaic films.
- How is PVDF raw material processed?
PVDF Raw Material can be processed using techniques such as extrusion, injection moulding, compression moulding, coating and lamination, and solution casting. Each processing technique offers unique advantages and is selected based on the desired properties and end-use requirements of the final product.
- What are the key properties of PVDF Material?
The key properties of PVDF material include exceptional chemical resistance, thermal stability, mechanical strength, and UV resistance. These properties make PVDF suitable for a wide range of applications in demanding environments, where performance and reliability are paramount.
- How can challenges in working with PVDF raw material be addressed?
Challenges such as high processing temperature, poor adhesion, crystallinity control, and environmental stress cracking can be addressed through various techniques, including optimising processing parameters, surface treatment, material selection, and component design modifications. These strategies ensure optimal performance and quality of PVDF-based products.