How Frequently Should Chemical Cleaning of Piping Systems Be Done?
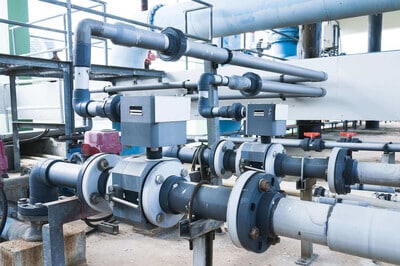
Industrial piping systems play a vital role in various sectors, including manufacturing, petrochemicals, energy production, and more. Over time, these systems can accumulate contaminants, scale, corrosion, and other substances that can affect their efficiency and integrity. Chemical cleaning, also known as chemical flushing or cleaning in place (CIP), is a maintenance procedure used to restore and maintain the performance of piping systems. In this blog, we’ll explore how frequently chemical cleaning of piping systems should be done and the factors that influence the cleaning schedule.
Factors Influencing the Frequency of Chemical Cleaning
The frequency of chemical cleaning for piping systems varies depending on several factors. Here are some key considerations:
- Type of Fluid Conveyed: The nature of the fluid running through the piping system is a significant factor. If the fluid is prone to fouling, scaling, or corrosion, more frequent cleaning may be necessary. For example, in industries dealing with corrosive chemicals, frequent cleaning is often required to prevent damage to the piping.
- Operating Conditions: The temperature, pressure, and flow rates within the piping system can impact the rate of scaling, fouling, and corrosion. High-temperature and high-pressure systems are more likely to experience accelerated fouling and may require more frequent cleaning.
- Water Quality: In cooling water systems or any system using water as a medium, the quality of the water source can affect the buildup of scale, deposits, and biological growth. Poor water quality may necessitate more frequent cleaning.
- System Design: The design of the piping system can influence its susceptibility to fouling and scaling. Dead legs, uneven flow distribution, or irregularly shaped piping can create areas where deposits are more likely to accumulate.
- Industry Regulations: Some industries, such as food and pharmaceuticals, are subject to strict hygiene and safety regulations. Compliance with these regulations may require regular cleaning and validation of the piping system.
- Maintenance History: Past maintenance practices and the history of fouling or scaling issues in the system can guide the cleaning schedule. If problems have been recurrent, more frequent cleaning may be needed.
- Economic Considerations: The cost of downtime and the cleaning process itself can influence the decision on how frequently chemical cleaning is performed. Balancing the cost of cleaning with the potential cost of inefficiency or system damage is essential.
Recommended Cleaning Frequencies
While the specific cleaning frequency varies based on the factors mentioned, here are some general guidelines for different types of piping systems:
- Heat Exchangers: Heat exchangers are prone to scaling due to temperature differences. They typically require cleaning every 6 to 12 months, although this can vary based on the quality of the heat transfer fluid and operating conditions.
- Boilers: Boilers should undergo chemical cleaning annually or when a significant decrease in efficiency is observed. The presence of scale can significantly reduce a boiler’s efficiency and lifespan.
- Cooling Towers: Cooling towers can accumulate scale and biological fouling. Routine cleaning, typically every 3 to 6 months, helps maintain their efficiency and prevent microbial growth.
- Process Piping: The cleaning frequency for process piping depends on the specific industry and the fluid being transported. In some cases, monthly or quarterly cleaning may be necessary to prevent contamination or product quality issues.
- Potable Water Systems: Potable water systems should undergo regular cleaning and disinfection, often annually or as recommended by local health regulations.
Monitoring and Inspection
Regular monitoring and inspection of piping systems are essential to determine when cleaning is necessary. Key indicators that may signal the need for chemical cleaning include:
- Reduced Flow: A noticeable decrease in flow rates or pressure drop across the system can indicate the presence of deposits or fouling.
- Reduced Heat Transfer: In heat exchangers or boilers, a drop in heat transfer efficiency suggests scaling.
- Corrosion or Leaks: Corrosion can lead to leaks or structural damage. Addressing corrosion issues promptly can prevent costly repairs or replacements.
- Water Quality: If water quality deteriorates, especially in potable water systems, it may be a sign of biological growth or contamination.
Conclusion:
The frequency of chemical cleaning for piping systems should be determined based on a combination of factors, including the type of fluid, operating conditions, water quality, and industry regulations. Regular monitoring and inspection are essential to identify when cleaning is required. Balancing the cost of cleaning with the potential costs of inefficiency, damage, or non-compliance is crucial in establishing an effective cleaning schedule. By following these guidelines and maintaining a proactive approach to cleaning, industries can ensure the longevity, efficiency, and reliability of their MAF pipe fittings and other piping systems.