How Does a Diaphragm Pump Compare to Other Types of Pumps?
Diaphragm pumps are often used for pumping liquids that contain solids or have a high viscosity. They also have high pumping capacity and can handle ...
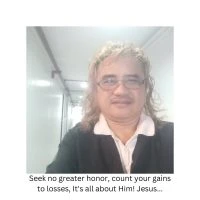
Diaphragm pumps are often used for pumping liquids that contain solids or have a high viscosity. They also have high pumping capacity and can handle ...