Do You Comply with OSHA? Investigating Key Safety Programmes.
The significance of providing a safe workplace cannot be overstated for both companies and employees. The Occupational Safety and Health Administration (
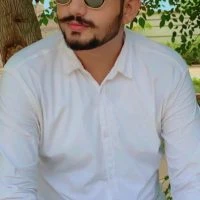
The significance of providing a safe workplace cannot be overstated for both companies and employees. The Occupational Safety and Health Administration (