Different Types of Seals Design
Austin Seal Company manufactures Teflon seals, molded & precision cut seals, o-rings and gaskets in elastomeric materials in Austin, TX
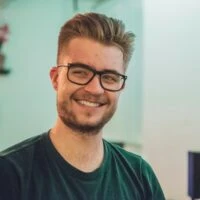
Austin Seal Company manufactures Teflon seals, molded & precision cut seals, o-rings and gaskets in elastomeric materials in Austin, TX