Benefits of Spliced O-Rings | Austin Seal CO
Austin Seal Company deals in high-tech industrial machinery and provides customized solutions and quality seals to their valuable clients. They provide industrial equipment like Kalrez, Gaskets, Spliced O-Rings, Parker and also provide special products and services to their valuable clients. They provide customized seals that are suitable for chemical, medical, aerospace, industrial, oil &gas, and beverages Industries. Customers can contact their sales or service department to get a quote for industrial equipment or prototyping or functional analysis of their product.
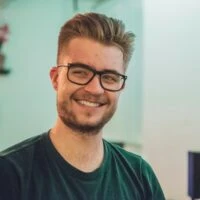