Asset Management and Material Surplus Solutions and Critical Work Stoppage & Aog Support
Asset management refers to the practice of managing a company\'s physical assets, such as equipment, real estate, and inventory, in a way that maximizes its ...
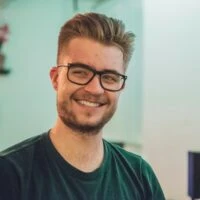