All About Nitinol Superelastic Spring
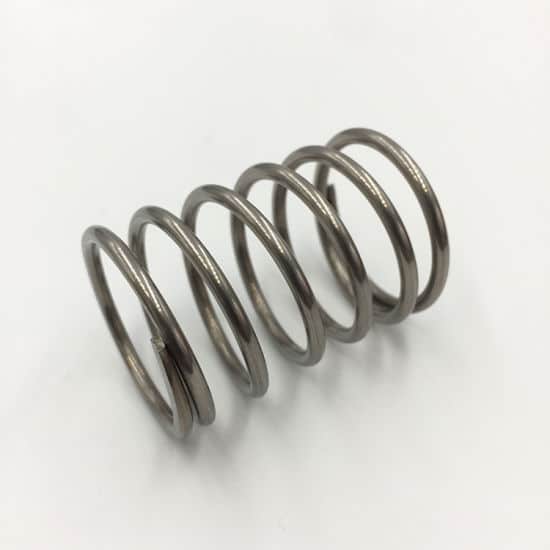
Nitinol Superelastic springs are extremely valuable in a variety of sectors since they possess all the properties of the Nitinol alloy. Thermally conductive and extremely tensile Nitinol Superelastic Spring are available. They are extremely capable of change. Springs made of nitinol superelastic have a high melting point. They have excellent thermal expansion properties, which increases their flexibility and elasticity. Superelastic springs made of nitinol have excellent corrosion resistance. They are strong and long-lasting due to their high resistivity. Because of their low permeability and susceptibility to magnetism, nitinol superelastic springs are ideal for medical applications. They are produced using a hot workability technique, which gives them ideal yield strength. Due to their capacity to quickly harden, cold workability is frequently difficult.
APPLICATIONS
- Nitinol tube is most commonly used to create self-expanding stents through laser cutting. In peripheral vascular applications, it is a popular option. When producing stents, concentration control and adequate surface polish of the tube’s inner diameter are essential for high yield. Along with other uses, nitinol tubes are also employed in orthopedics, endoscopy, and biopsy.
- Catheters are guided into the body’s hard-to-reach spaces using nitinol guidewires.
- They are advantageous because, in contrast to stainless steel, they are kink resistant. Since the wire is elastic, it can move through the body in any direction without suffering any harm.
- Nitinol will provide torque and rotate smoothly. Braided stents and filters are frequently made using nitinol wires.
- Because it allows for flat product creation and subsequent shaping to create devices, nitinol sheet is desirable because it provides design flexibility not possible with other forms.
- It is possible to make sheets with very small thickness tolerances and thickness control that are homogeneous across the surface. With uniform beginning sheet thickness and controlled post-processing, the final dimensions will be predictable thanks to this high process capacity.
- Nitinol has the disadvantage of not being radio-opaque, which is necessary for stent insertion and the ability to find the device inside the body.
- To increase radio-opacity, various marking systems consisting of precious metals, such as platinum and palladium, are frequently utilized in conjunction with Nitinol-based devices.
PROCESSING
- Vacuum induction melting and vacuum arc remelting are used to melt nitinol ingots. To develop intermediate forms that are later manufactured into bars, coils, and plates, billets are forged and hot rolled. Plates are rolled down to create a thinner sheet, and coils are further drawn to create wires with lower diameters. Gun-drilled bars are used to make “tube hollows” that are later pulled into tubes. Drilling into guns is a necessary evil. Because it loses a sizeable proportion of nonrecoverable material, like bar weight versus tube hollow weight, it instantly lowers the process’s effective yield.
- Due to the development of titanium oxides and carbides, it is crucial to regulate the amount of oxygen and carbon in the melt. These substantial inclusions function as breaks in the matrix
- To give the material the appropriate qualities, thermomechanical processing a combination of cold working and heat treatment is essential.
- Nitinol alloys work to harden extremely quickly during cold working fabrication procedures like drawing or rolling. After a certain amount of cold work, if the material is not annealed, the strength increases to the point where further deformation causes the fracture strength to be attained, which leads to failure.
- The Nitinol component’s final shape is also established by heat treatment. Temperatures of 400° to 500°C with the proper dwell periods will produce a straight, flat, or shaped component if the Nitinol has a reasonable amount of cold work in it (of the order of 30% or more).
- This procedure, known as “shape setting,” makes use of custom fixtures to produce shaped parts. Strand annealing (for straight wire and tubing), box furnaces, molten salt baths, and fluidized beds are a few typical heat treatment techniques.