Achieving High Vacuum Levels With a Micro Air Compressor
In this article we\'ll look at a couple of methods you can use to boost the vacuum levels you get from a micro air compressor. ...
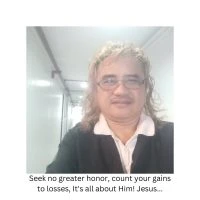
In this article we\'ll look at a couple of methods you can use to boost the vacuum levels you get from a micro air compressor. ...