A Comprehensive Guide to Know About Varied Transformer Testing Equipment
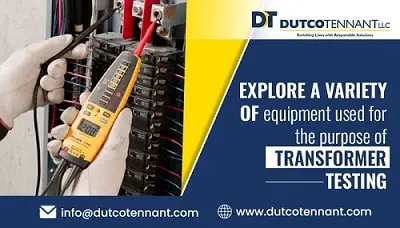
Behind every electrical system’s uninterrupted performance lies the contribution of transformers. These unsung champions ensure electricity flows seamlessly across voltage realms, powering our lives.
As these devices play a pivotal role in power infrastructure, ensuring their reliability and performance is of utmost importance. Transformer testing is an essential aspect of maintenance and quality assurance. And with the use of the right transformer testing equipment, this goal can be achieved.
In this comprehensive guide, we explore different equipment in use for transformer testing and cover other key aspects of them. Read through the end to learn all the details.
Introduction to Transformer Testing Equipment
Transformer testing equipment encompasses a wide range of instruments designed to assess the condition, performance, and safety of transformers. These tests are conducted during manufacturing, installation, and regular maintenance to detect any potential issues and ensure optimal functionality. The main types of transformer testing equipment can be categorised as follows:
1. Electrical Testing Equipment
Turns Ratio Testers: These devices measure the turns ratio of the transformer windings to ensure proper voltage transformation. Any deviation from the expected ratio can indicate winding defects or misconnections.
Winding Resistance Testers: Winding resistance testers assess the resistance of transformer windings, identifying any discrepancies that might lead to energy losses or overheating.
Insulation Resistance Testers: These testers evaluate the insulation resistance between the transformer’s windings and its core. Low insulation resistance can signify insulation deterioration or moisture ingress.
Partial Discharge Testers: Partial discharge testing detects low-level discharges within the transformer, helping to predict potential insulation failures.
2. Dissipation Factor Test Equipment
Tan Delta Testers: Tan delta, also known as the dissipation factor, measures the power loss in the transformer insulation. High tan delta values indicate deteriorated insulation quality.
3. Oil Testing Equipment
Dielectric Strength Testers: Dielectric strength testers assess the insulating oil’s ability to withstand high voltage. Degraded oil can lead to decreased transformer performance and safety.
Moisture Analyzers: Moisture analyzers detect the presence of moisture in transformer oil, preventing insulation breakdown and internal faults.
Gas Chromatographs: Gas chromatographs identify the concentration of dissolved gases in transformer oil. Abnormal gas levels can indicate overheating or internal arcing.
4. Mechanical Testing Equipment
Vibration Analyzers: Vibration analyzers detect mechanical vibrations in transformers, which can indicate loose connections, structural issues, or impending failures.
Noise Level Meters: Noise level meters measure acoustic emissions from transformers. Unusual noise patterns may suggest loose windings or core laminations.
The Chronicles of Transformer Testing: Why Does It Matter?
Now that we have the standard idea of transformer testing equipment, let’s explore the reasons why they are intended to be used. In the world of magic, a staff’s quality can mean victory or defeat. Similarly, the quality of transformers can mean efficient power systems or costly disasters. Transformer Testing Equipment ensures victory.
Quality Assurance
Every wizard takes pride in their spellbook. Likewise, manufacturers take pride in their transformers. Transformer Testing Equipment ensures each one adheres to standards, ready to wield their magic in the domain of power transmission.
Preventive Maintenance
Wizards study signs to predict events. Transformer testing reads the signs within transformers, predicting potential problems. It’s the guardian who prevents disasters by nipping them in the bud.
Safety
Heroes protect lives; so do transformers. Faulty ones, however, pose dangers. Transformer testing detects weak points, fortifying these sentinels to guard us against catastrophic failures.
Efficiency
In magic, every spell requires energy. In transformers, energy loss can be costly. Transformer testing minimises these losses, enchanting transformers to be more efficient in their duties.
Performance Optimisation
Unfortunately in the real world, you cannot just assume to identify failures. Precisely why transformer testing equipment are no less than magic as they help detect problems such as winding defects or core issues. Resulting in taking corrective actions that enhance transformer performance.
Challenges and Innovations
While traditional transformer testing methods have been effective, the industry is witnessing advancements in testing equipment:
- Online Monitoring: Continuous online monitoring systems allow real-time assessment of transformer conditions, enabling prompt responses to anomalies.
- Dissolved Gas Analysis (DGA) Sensors: Miniaturised DGA sensors offer quicker and more frequent monitoring of gas levels in transformer oil, providing insights into potential faults.
- Digital Twin Technology: Digital twin models simulate transformer behaviour, facilitating predictive maintenance. They analyse real-time data against the model’s predictions.
Conclusion
Transformers are the unsung heroes of the modern age. They channel energy, illuminate lives, and power progress. But these heroes need their gear checked and spirits aligned.
Transformer Testing Equipment is the key to this endeavour, ensuring our heroes stand tall, ready to light up our world for generations to come. So remember, next time you flick that switch, it’s not just power flowing – it’s magic, it’s innovation, and it’s the legacy of transformer testing equipment.
If you are looking for a trusted supplier to get your hands on high-quality transformer testing equipments then check out Dutco Tennant LLC. Over the years, they have delivered top-of-the-line products for large scale projects in the UAE.