How Are SS Forged Pipe Fittings Made?
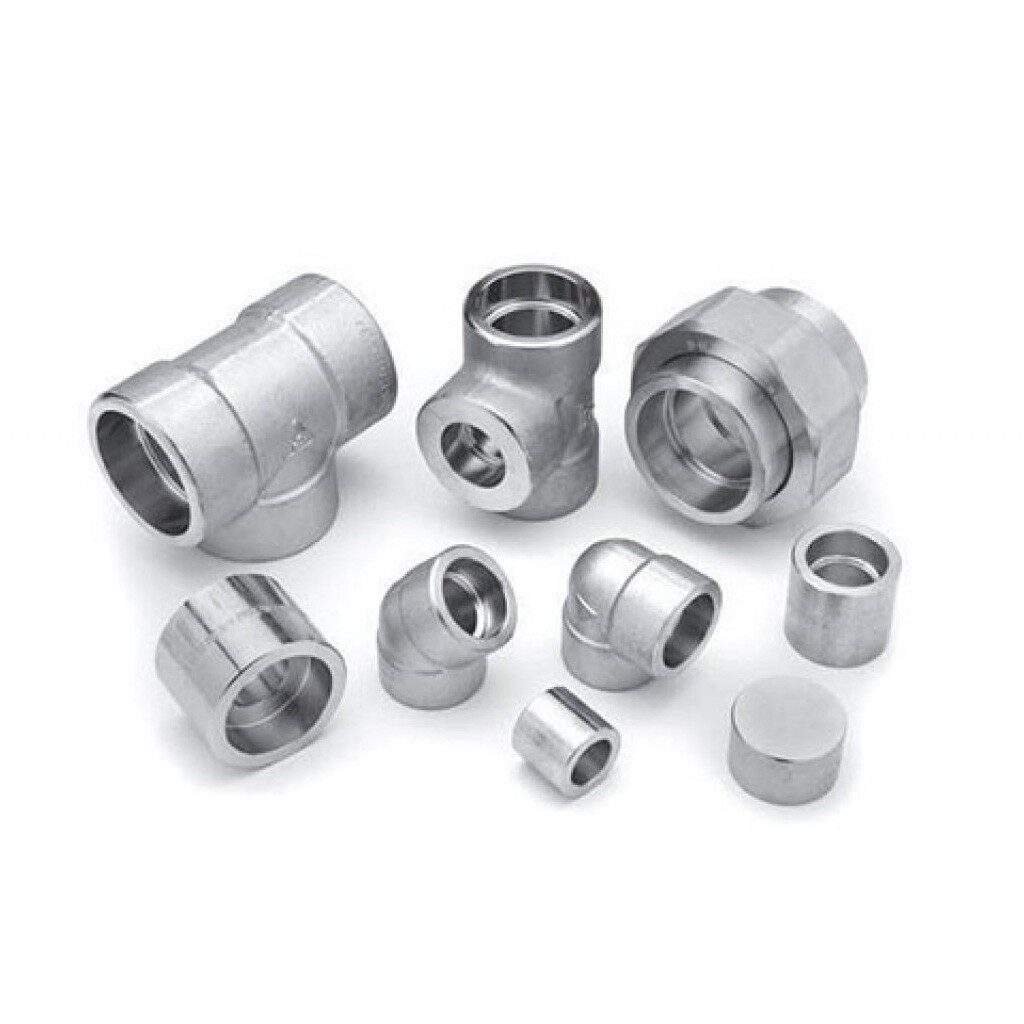
Pipe Fittings are components used in plumbing that support the direction of flow in adjustments like elbows and tees. Alters the tubing’s size, such as reducers and rising tees. Connect various elements, like couplings, and disrupt flows, like caps.
Regular fittings are either cast or hammered. The only type of pipe used to create wrought fittings is seamless. The device produces welded fittings with a large diameter. Stainless Steel Forged pipe fittings (Socket Weld and Threaded) are used to connect pipes and pipelines for the nominal bore schedules. They are produced following the ASME B16.11, MSS SP-79, 83, 95, and 97, and BS3799 standards. There are threaded pipe fittings and socket weld pipe fittings available for forged iron pipes.
Manufacturing Procedures for Forged Fittings
Elbow, Tee, Reducers, and other pipe fittings are made using a variety of manufacturing techniques. Stainless Steel Forged Fittings are created using smooth pipe and welded steel as filling materials (ERW & EFW pipes cannot be used for constructed fittings). There are created large diameter Plate fittings. The following are a few of the several procedures utilized in the production of the forged pipe fittings: Deep Drawing Method for caps, Hydraulic Bulge Method – Cold forming, Hot forming, or Extrusion Method, and Flare Method for Stub Ends.
Double weld seam Method: One of the methods frequently employed is to create elbows out of tiles. Each pair of raw material tiles is forced and welded together after being symmetrically sliced into two pieces. This method can be applied to a variety of materials and even big items with a diameter of over one meter. It has two seams and cutting-edge welding technology in use to satisfy various global needs.
Flare Method for Stub ends: Flaring is used to create Stub Ends or Lap Joint Flange. A flare or flange face cut-off is a flow termination. Stub ends are frequently created during welding after the forge block is machined to the desired size.