How Do You Choose Rubber Seals & Gaskets for Industrial Application?
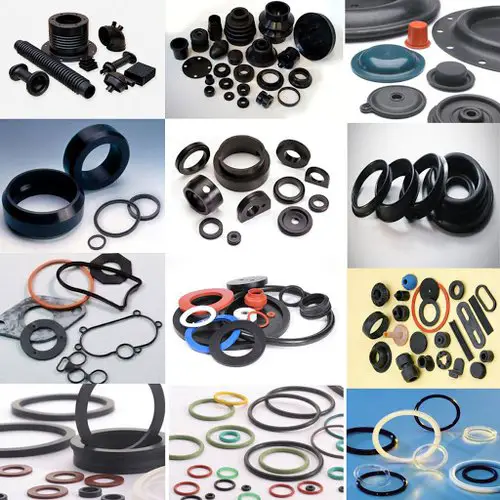
Fluid leakage, such as liquids and gases, is a major concern in many businesses as they are used in many industrial processes. Silicone Profile Gasket Manufacturer and Supplier use various types of rubber seals and gaskets in equipment responsible for the transport of these fluids to avoid this. Rubber seals have thus become an essential component of valves, pumps, pipe fittings, and vacuum seals. Does this imply that all rubber seals are identical? No, they aren’t all made equal.
They differ in terms of design, materials, and other features. As a result, numerous considerations must be made while developing seals for industrial applications. A few crucial elements to consider when making rubber seals and gaskets are outlined in this article. When designing rubber seals and gaskets, there are a few things to keep in mind. The following points will assist you in making the best decision possible regarding these seals:
Environment of Use: You could agree that replacing gaskets on a regular basis can be time-consuming and frustrating. To avoid this, it’s crucial to think about the setting in which they’ll be situated. Materials for Silicone Inflatable Gasket Manufacturer have numerous limits in businesses including the military, food, and pharmaceuticals. The following factors should be taken into account:
- The influence of pressure and temperature on the seals
- Compatibility with the chemicals to be utilised
- Friction has the potential to cause excessive pressures to build up and rupture the seal section.
- Different portions of the seal’s tolerance stack up.
Requirements in terms of dimensions: What is the definition of a proper seal? What causes it to happen? When a seal is compressed between two surfaces, it seals. The compression generates deformation, which aids in the prevention of fluid loss. The seal’s cross-section must be greater than its gland depth to achieve this deformation or correct compression. The seal may not compress adequately or rupture the connection between the two mating surfaces if the cross-section is too tiny or too large.
Consider the Adhesive Attachment System: Always make sure the attachment surface is 1/8 inch broader than the attachment surface. The adhesive must be applied to the substrate’s and seal’s flat surfaces. When creating a rubber seal for your application, Silicone Tube Manufacturer In India must be considered the thickness of the adhesive products.
Total Amount of Load Applied: What is the total amount of load applied? If the load applied is greater or lesser than what is specified, the consequences can be disappointing. The overall amount of force exerted can be easily regulated by manipulating the cross-shape sections or by adding hollow sections or holes.
Required Closing Force: What is the application’s needed closing force? How much closing force will the application tolerate? If a seal is designed to withstand a maximum of 20 pounds of force, it is not suitable for use in a situation where it may be subjected to 50 pounds of force. You must also consider the force required on the seal, the surface area, and the cross-sectional dimension.
Friction Forms to Expect: When it comes to dynamic movement applications, there are two types of friction to expect: breakout friction and running friction. If the part movement is irregular, the breakout friction might lead to high pressures. Running friction, on the other hand, can cause heat to build up, which can lead to swelling. Friction can induce seal failure in both circumstances.
Rubber gaskets and seals in various specifications have been provided by the Silicone Transparent Tube Manufacturer in India to fulfil the needs of difficult applications.
All of these considerations will aid you in achieving optimal sealing performance. If you are unable to make a decision, it is always best to contact Best Rubber Products Manufacturers, such as Rekson, who will assist you in making the best choice.