Understanding Eddy Current Testing for Defect Evaluation Applications
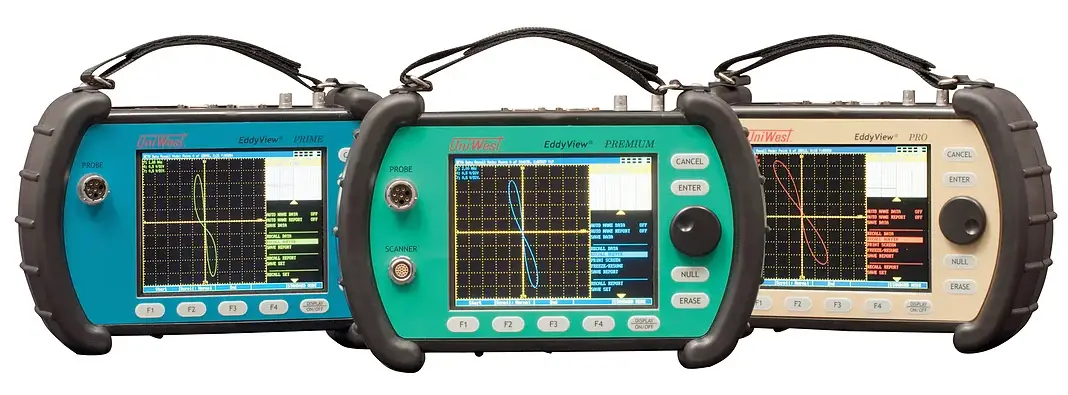
Non-destructive testing methods are popular in the industrial sector for various purposes. There are different methods under non-destructive testing that help evaluate the thickness and coating measurements, flaw detection, and much more. One such method is the eddy current testing that uses electromagnetism for flaw detection.
What is Eddy Current testing?
This non-destructive testing method uses the electromagnetic induction principle to detect the surface and subsurface flaws in conductive materials like copper. Although this technique is decades old but with advancement in the test procedures, the efficiency of test results has improved a lot.
With the help of this method, cracks under the surfaces or potential corrosions can be detected well on time. These results help take necessary actions to prevent any hazards. Moreover, it helps select quality materials meeting the industrial demand.
How eddy current testing works?
The probe used in this form of testing has a wire coil in which the alternating current flows. The flow of electric current creates the magnetic field, and when this coil gets in contact with the object, it creates an eddy current. With the fall and rise of alternating current, the magnetic field expands and contracts. If the flow of eddy current is stopped or interrupted, it is a sign of a crack or corrosion building up in the object.
A trained professional can then figure out the defect and its intensity based on the changes in phase angle and ratio of current and voltage amplitude. If a larger area is to be covered, one needs several coils with an array of eddy currents.
Advantages of Eddy Current Testing
This non-destructive testing technique has many benefits.
- This technique can help detect cracks that are as small as 0.5mm in thickness.
- The equipment used is portable, which allows performing the testing procedure at any location.
- It can efficiently detect the flaws through several layers, including those having non-conductive surface coatings.
- Even the objects with complex formulation can get tested with utmost efficiency.
Eddy current testing is one of the most efficient and reliable non-destructive testing techniques for flaw detection on conductive materials. Over the years, experts have introduced various ways, and different equipment has come into the market, ensuring accuracy. One must choose the best sellers to buy the equipment to ensure efficiency.
About the author
PCTE Industrial is a specialist in the sale and hire of industrial non-destructive testing (NDT) equipment. PCTE INDT is a branch of PCTE, who has been serving in the NDT industry since 2008.We offer a range of INDT equipment that covers the bread and butter applications but also adds some exciting technology. Our range covers devices for Ultrasonic Testing (UT), Eddy Current (ET), Magnetic Particle (MT), Dye Penetrant (DT) and Visual Testing (VT).