Understanding the Different Finishes of Aluminum Sheets – Inox Steel India
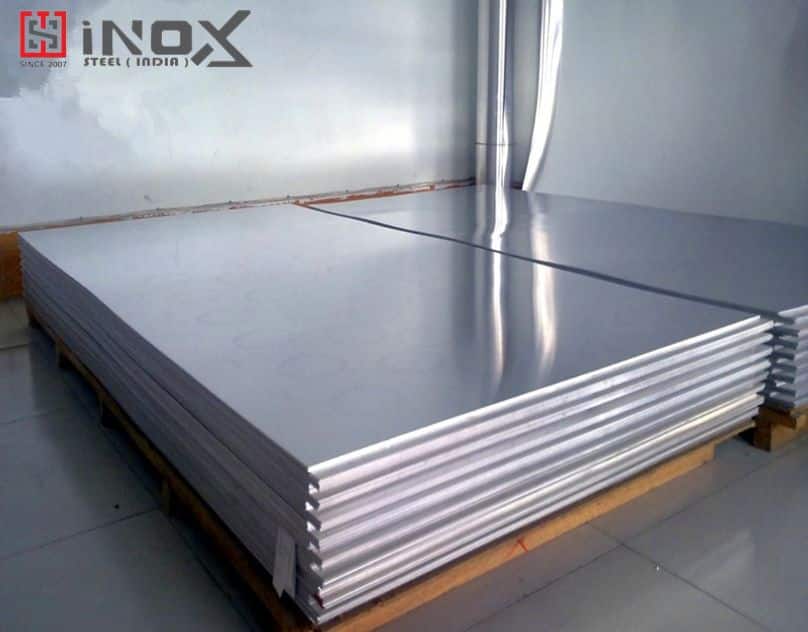
Inox Steel India, a highly respected player in the Aluminium Sheet manufacturers in India, has earned widespread acclaim for its exceptional products. Renowned for their remarkable corrosion resistance, aluminum sheets are a durable and long-lasting choice, making them ideal for environments susceptible to moisture and other damaging elements.
As a prominent aluminium Sheet suppliers in India, we have built a strong reputation. Our manufacturing process involves melting the metal, casting it into ingots, and then rolling it into thin, high-quality sheets. The exceptional properties of aluminum have made it a highly sought-after material across various industries, solidifying our position as a leading aluminum sheet supplier in Chennai.
Our top-quality aluminum sheets can be found in cities like aluminium sheet supplier in Faridabad and aluminium sheet supplier in Pune, showcasing our commitment to providing reliable and advanced aluminium solutions. We take great pride in utilizing cutting-edge technology to produce aluminium sheets that are renowned for their strength, exceptional quality, and durability. As a trusted Aluminium Sheet manufacturer, we are dedicated to meeting the unique needs of our valued customers.
Aluminum is an incredibly adaptable and prevalent metal, utilized across numerous industries, from building to automobiles, electronics to consumer products. A crucial element in working with aluminum is recognizing its diverse surface treatments, which can dramatically affect the metal’s visual appeal, functionality, and practical uses. This article aims to offer a thorough examination of the various finishes accessible for aluminum sheets, empowering you to make an informed decision that best suits your unique requirements.
The Importance of Aluminum Finishes
Polishing aluminum is vital for various reasons. It can boost the metal’s visual appeal, shield it from corrosion, strengthen its resilience, and modify its surface attributes to better fit specific uses. Whether you employ aluminum for structural, decorative, or functional needs, picking the right finish can greatly impact the final product’s efficiency and lifespan.
Common Aluminum Sheet Finishes
Mill Finish
The raw, unprocessed look of aluminum, just as it emerges from the rolling mill, is known as the mill finish. This finish features a glossy, mirror-like surface with visible marks and imperfections left over from the rolling process. Although it is the most affordable and simplest option, mill finish aluminum is appropriate for uses where visual appeal is not the main priority. It is frequently utilized in construction projects, where the aluminum will be painted or concealed in some other way.
Brushed Finish
The aluminum surface is transformed through a process that involves abrasive belts or brushes, resulting in a uniform, satin-like finish. This technique helps eliminate any surface flaws, giving the aluminum a matte and textured look. Brushed aluminum is widely used in decorative settings, like kitchen appliances, vehicle trims, and architectural features, as it provides a sleek and contemporary aesthetic. Furthermore, the brushed texture can effectively conceal fingerprints and minor scratches, making it a practical choice.
Anodized Finish
Anodizing is an electrochemical technique that strengthens the natural protective layer on the surface of aluminum. This process improves the material’s resistance to corrosion and wear, creating a more resilient and visually appealing finish. Anodized aluminum can be colored in diverse hues, allowing for greater design versatility. This surface treatment is widely utilized in consumer electronics, building exteriors, and interior décor applications.
Polished Finish
Gleaming aluminum, meticulously polished, boasts a mirror-like sheen accomplished through mechanical techniques. This lustrous finish is attained by progressively employing increasingly fine abrasives and polishing compounds until a reflective surface is reached. Polished aluminum is frequently utilized in decorative settings, including signage, automotive parts, and premium appliances, where a powerful visual impression is sought.
Flexible aluminum sheets have become a go-to choice across various industries, catering to a broad spectrum of requirements.
The 7075 aluminum sheet manufacturers in India, have earned a trusted name for themselves in diverse sectors. These manufacturers make essential contributions to the nation’s industrial advancement, solidifying their standing as leading players in the field.
India is a thriving hub that hosts a wide range of industries, including construction, automobile, packaging, and aerospace As we are the top 1200 Aluminium sheet manufacturers in India, established a solid reputation for creating products renowned for their exceptional durability and resilience.
India’s 5052 aluminum sheet manufacturer, known for their dependability and credibility, are a source of pride for the country. These companies’ unwavering dedication to providing exceptional goods has been a key driver in the industry’s progress.
Prominent Indian enterprises spearheading the 6082 aluminum sheet industry are committed to harnessing state-of-the-art technology and manufacturing methods, ensuring their products consistently meet the most stringent quality and performance standards.
Countless places offer an abundance of vendors selling aluminum panels.
Powder Coated Finish
Aluminum surfaces can be transformed through a specialized process called powder coating. This technique involves coating the metal with a dry powder, which is then baked under heat to create a strong, protective finish. The resulting layer comes in diverse colors and textures, offering superior resistance to corrosion and exceptional longevity. Powder-coated aluminum is particularly well-suited for outdoor uses, like patio furnishings, fencing, and automotive components, as it can endure challenging environmental conditions.
Painted Finish
Painted aluminum involves applying liquid paint to the aluminum surface, followed by curing to create a durable coating. This finish offers a broader range of color options and can include additional protective layers for enhanced durability. Vibrant aluminum panels have become a versatile choice for architectural projects, signage, and decorative elements, where visually appealing colors and aesthetics are paramount. These painted aluminum sheets offer a diverse range of hues and finishes that can enhance the visual appeal of various structures and installations.
Textured Finish
Textured finishes are achieved through various mechanical processes, such as embossing, hammering, or sandblasting, to create a patterned or rough surface on the aluminum sheet. These finishes not only enhance the visual appeal but also provide functional benefits, such as improved grip and reduced glare. Textured aluminum is often used in flooring, wall panels, and industrial applications.
Chemical Finishes
Chemical finishes involve treating the aluminum surface with specific chemicals to achieve desired properties. Common chemical finishes include etching, passivation, and conversion coatings. These treatments can improve corrosion resistance, adhesion for subsequent coatings, and surface appearance. Chemical finishes are widely used in the aerospace, automotive, and electronic industries.
Choosing the Right Finish
Selecting the appropriate finish for aluminum sheets depends on several factors, including the intended application, environmental conditions, desired appearance, and budget. Here are a few considerations to keep in mind:
- Application: Functional requirements should drive the choice of finish. For example, anodized or powder-coated finishes are ideal for outdoor use due to their excellent corrosion resistance.
- Aesthetic Appeal: If appearance is a primary concern, finishes like polished, brushed, or painted aluminum offer various options to achieve the desired look.
- Durability: Consider the environmental conditions the aluminum will be exposed to. Anodized and powder-coated finishes provide superior durability in harsh environments.
- Cost: Budget constraints may influence the choice of finish. Mill finish is the most cost-effective, while specialized finishes like anodizing or polishing can be more expensive.
Aluminum Weight Charts – Inox Steel India
These charts come in handy when it comes to calculating the weight of various aluminum products like sheets, plates, angles, and pipes. They also assist in organizing and selecting aluminum plates. Engineers and fabricators can effortlessly locate appropriate aluminum plates that meet their specific needs by categorizing the plates based on their dimensions and thickness.
To know more, visit:
Our website: inoxsteelindia.net