Actuator valve: A Crucial Component in Modern Industry
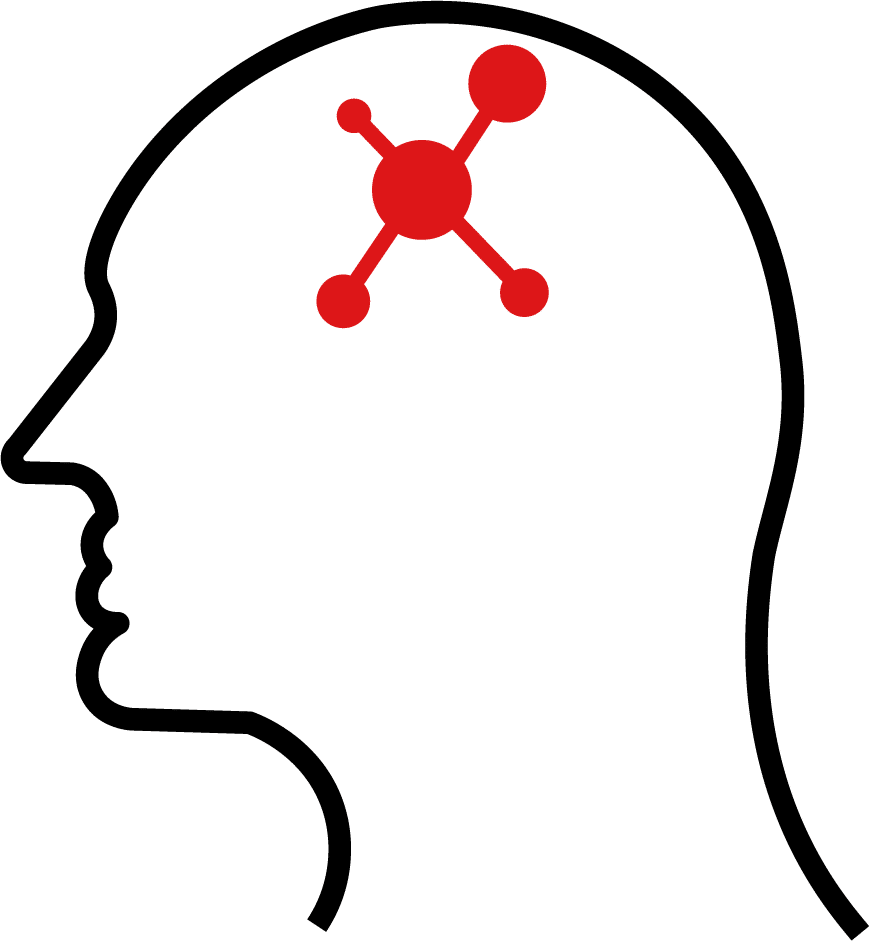
Introduction
The actuator valve is a type of valve that has become an essential component in various industries, including oil and gas, chemical processing, and water treatment. Its unique design and functionality make it an ideal choice for controlling the flow of fluids, gases, and slurries. In this article, we will delve into the world of ball valves, exploring their history, design, types, applications, and benefits.
History of actuator valve
The actuator valve has its roots in the early 20th century, when engineers began experimenting with new valve designs to improve flow control and reduce pressure drop. The first ball valve was patented in the 1950s, and since then, it has undergone significant improvements, becoming a staple in modern industry. More information
Design and Functionality
A actuator valve consists of a spherical ball with a hole in the center, which rotates to control the flow of fluid. The ball is typically made of metal or ceramic materials, and is surrounded by a valve body, stem, and actuator. The valve body is the main structure that houses the ball, while the stem connects the ball to the actuator, which is responsible for rotating the ball.
The actuator valve operates by rotating the ball to align the hole with the flow path, allowing fluid to flow through. When the ball is rotated 90 degrees, the hole is perpendicular to the flow path, blocking the flow of fluid. This simple yet effective design makes the ball valve an ideal choice for controlling fluid flow.
Types of actuator valve
There are several types of ball valves, each designed for specific applications:
Full Port actuator valve: These valves have a full-bore design, allowing for maximum flow rates and minimizing pressure drop.
Reduced Port Ball Valves: These valves have a reduced-bore design, which reduces the flow rate but increases the pressure rating.
V-Ball Valves: These valves have a V-shaped ball, which provides a more precise control over fluid flow.
Ceramic Ball Valves: These valves have a ceramic ball, which provides excellent corrosion resistance and is ideal for harsh environments.
Applications of Actuator valve
Actuator valve is used in a wide range of industries, including:
Oil and Gas: Ball valves are used to control the flow of oil, gas, and petrochemicals in pipelines and processing facilities.
Chemical Processing: Ball valves are used to control the flow of corrosive chemicals and hazardous materials in chemical plants.
Water Treatment: Ball valves are used to control the flow of water and wastewater in treatment plants and distribution systems.
Power Generation: Ball valves are used to control the flow of steam and water in power plants.
Benefits of actuator valve
Actuator valve offer several benefits, including:
High Flow Rates: Ball valves can handle high flow rates, making them ideal for applications where fluid flow needs to be maximized.
Low Pressure Drop: Ball valves have a low pressure drop, which reduces energy losses and increases system efficiency.
Corrosion Resistance: Ball valves can be made from corrosion-resistant materials, making them ideal for harsh environments.
Easy Maintenance: Ball valves are relatively easy to maintain and repair, reducing downtime and increasing system reliability.
Conclusion
The actuator valve is a crucial component in modern industry, providing a reliable and efficient means of controlling fluid flow. Its unique design and functionality make it an ideal choice for a wide range of applications, from oil and gas to water treatment and power generation. By understanding the types, applications, and benefits of ball valves, engineers and technicians can design and operate more efficient and reliable systems.
https://notebook.zohopublic.com/public/notes/99kl98504f4434d9b4282937fef675107b2fe |