Common Mistakes to Avoid When Working with Pipes and Tubes
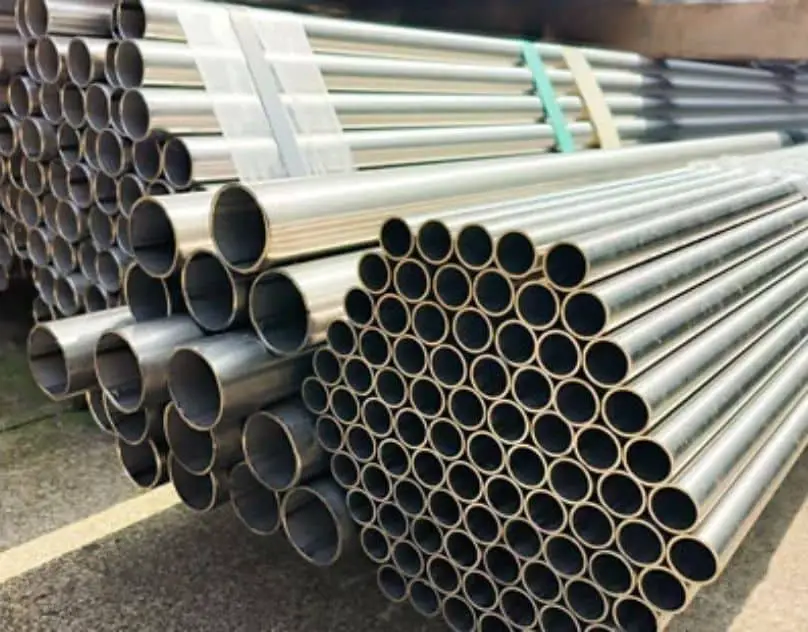
Working with pipes and tubes is an essential skill in many sectors, including building, manufacturing, and plumbing. To preserve the efficiency and duration of your projects, avoid typical errors that might result in costly repairs and safety risks. In this message, we will look at the most common faults and offer advice on how to avoid them.
Improper Material Selection
Selecting the appropriate material is essential when handling pipes and tubes. Certain material qualities are needed for each application, and choosing the incorrect kind might result in early failure.
Not Considering Environmental Factors
The environment in which the pipes and tubes will be utilized is an important consideration when selecting materials. For example, stainless steel is good for corrosive situations, but carbon steel is better suited to high-pressure applications. Failure to address these issues can lead to corrosion, leaks, and structural problems.
Ignoring Temperature and Pressure Requirements
Every material has a specific range of temperature and pressure it can withstand. Using a material outside its designated range can compromise its structural integrity. Always verify that the selected material meets the project’s temperature and pressure requirements.
Inadequate Sizing and Design
Incorrect Pipe Diameter
Using pipes with inappropriate sizes can cause a variety of problems, including lower flow rates and higher pressure drops. It is critical to calculate the proper diameter depending on the application’s flow needs and pressure conditions.
Improper Wall Thickness
In order to make sure the pipe can withstand the internal pressure, wall thickness is essential. While too thick walls might be unnecessarily costly, insufficiently thick walls can cause pipes to break down. To find the proper wall thickness, use industry norms and recommendations.
Poor Installation Practices
Inappropriate Joint Connections
Leaks and faults are frequently caused by faulty joint connections. The system as a whole may be compromised by using the incorrect kind of joint or using incorrect installation methods. Make sure that every joint is positioned, sealed, and tightened in accordance with the manufacturer’s instructions.
Lack Of Sufficient Support And Bracing
It is necessary to provide sufficient support and bracing for pipes and tubes to avoid drooping, shifting, and vibrating. Failure and stress fractures might result from inadequate support. When installing and spacing supports and braces, adhere to industry norms.
Neglecting Regular Maintenance
Failure to Perform Routine Inspections
Regular inspections are crucial for identifying potential issues before they become major problems. Develop a maintenance schedule that includes routine checks for leaks, corrosion, and other signs of wear and tear.
Ignoring Small Leaks and Corrosion
Small leaks and early signs of corrosion can quickly escalate into significant issues if not addressed promptly. Implement a proactive maintenance approach to repair these problems as soon as they are detected.
Using Substandard Products
Opting for Low-Quality Materials
While it may be tempting to save money by choosing cheaper materials, this method might result in considerable long-term expenses. Low-quality pipes and tubes are more likely to fail and may not exceed required safety requirements. Invest in high-quality materials from recognized vendors to ensure the durability and dependability of your projects.
Failing to Verify Product Specifications
Make sure the goods you are utilizing fit the project’s parameters every time. Verifying material grades, dimensions, and performance attributes is part of this. Utilizing goods that don’t fit the requirements puts the system as a whole at risk.
Top-rated Pipes and Tubes Manufacturers in India
Sagar Steel Corporation is one of the most excellent Pipes and Tubes Suppliers in India. In many sectors, including construction, oil & gas, automobile, and more, pipes and tubes are essential. These parts perform vital tasks including supporting structural integrity and moving gasses and liquids. India’s manufacturing industry is booming, and its high-quality pipes and tubes are contributing significantly to the worldwide market. This article explores the leading Indian manufacturers, their inventions, and the effect they have on the market.
India’s pipe and tube manufacture began in the early twentieth century. Initially, the business relied significantly on imports to supply domestic demand. However, with the onset of industrialization, local manufacturing began to emerge, signaling the start of a self-sufficient industry.
Modern society relies on pipes and tubes to support a variety of industrial processes and common infrastructure systems. Their versatility transcends many industrial boundaries, including energy, construction, healthcare, and telecommunications. As we continue to innovate and transform, it is imperative that we recognize and respect the significant role that manufacturers of pipes and tubes play in furthering progress and affecting the world around us.
India’s industrial progress is dependent on the efficiency of its components. Discover how Indian Pipes and Tubes Manufacturers contribute considerably to the country’s industrial environment, providing varied industries such as construction and petrochemicals.
As an industry pioneer, we believe that our unique products, such as Round Bars Manufacturer and Fasteners Manufacturer in India, should thoroughly benefit our clients.
For More Detail
Website: sagarsteel.net
Product: Pipes and Tubes Manufacturer in India
Other Product: Flange Manufacturer In India.