How to deal with the fluctuation of supply and demand of chemical products
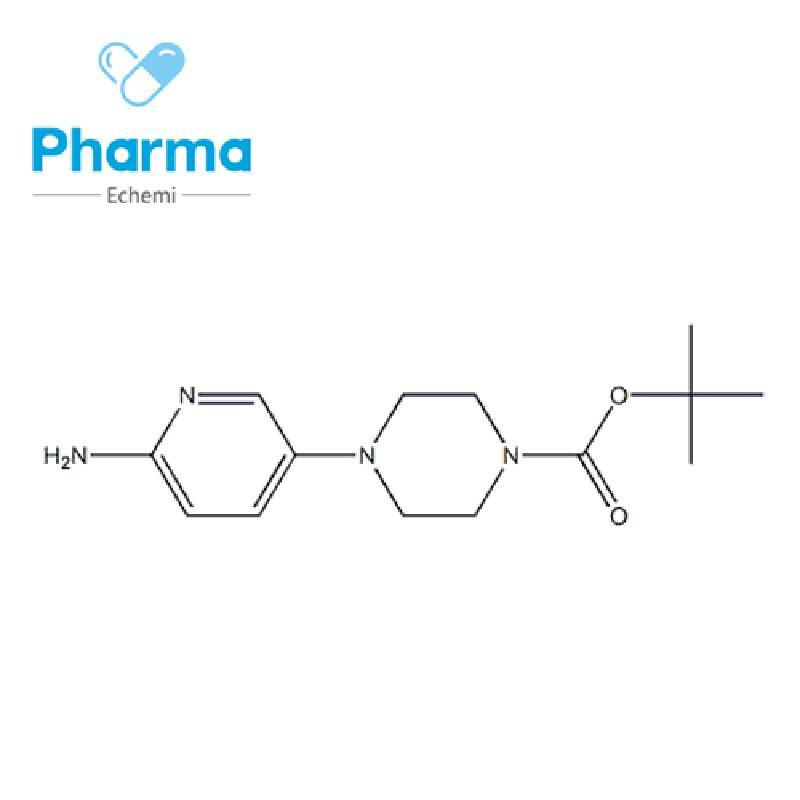
The huge scale of the chemical industry makes it a complex whole; there are many things to manage. Chemical industry often has to cope with huge fluctuations in supply and demand. These fluctuations may be due to market volatility, lack of raw materials or changes in customer demand. To properly address these issues, it is essential to make your delivery lines work freely.
For example, when you send the goods to the customer location, there are many fuzzy visible areas in the middle. Its delivery is usually confirmed only when the customer uninstalls it and sends it back for confirmation. As a result, your returnable assets are often waiting in the customer’s location.
This situation prevents you from making the most of your recyclable assets in your chemical products supply chain. You can’t complete several orders because your team doesn’t know when your returnable assets will return to your warehouse or you may have too many returnable packages in stock.
It limits your timely delivery of your chemical products, causing confusion. You rely heavily on your customer or fleet manager to confirm the status of the container. If you know where your returnable assets are, you can optimize delivery.
If your truck driver knows that empty containers lie in the customer’s location, if the location is on their route, they can take them. This will accelerate the reverse flow of your assets.
Solution:
The use of advanced fourth generation supply chain control tower can solve the problem of supply and demand fluctuation.
It will serve as a center to provide all information about your returnable assets, ongoing deliveries, and even planned deliveries.
The fourth generation supply chain control tower is not passive response, but predicts supply interruption in advance.
It provides excellent real-time visibility, along with operational data and insights about your chemical products supply chain. The control tower analyzes the data and makes the model for reference. When AI (Artificial Intelligence) discovers a deviation in a typical pattern, it warns you and tells you what you can do to correct it. This kind of artificial intelligence is trained according to the data of multimodal transport industry for many years.
For example, if your warehouse lacks recyclable containers, the control tower can alert you of a supply bottleneck. You can get the following insights from such a system:
Uncertainty of delivery time
Residence time for each asset, type of asset, and single location
Delivery of raw materials
Your delivery speed
Delivery time depends on site location data and other conditions
System throughput – it takes into account factors such as manufacturing, distribution, and delivery
Insight into the interrupt results
Automation is extremely low