What Is Soldering Wetting and Why Is It Important?
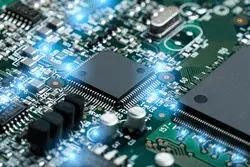
Even the most experienced manufacturers struggle with bad solder junctions. The root reason may be difficult to identify. But the real cause is frequently a subpar soldering wetting procedure.
We provide a 101 overview of the solder-wetting procedure in this post. You may create soldering junctions that last the test of time by using our tried-and-true advice to help you avoid insufficient wetting. If you wish to be a professional and expert technician, then undergoing IPC a-610 certification program can be of great help that will help your company manufacture the right quality products as you know the set standards of quality, acceptance, and compliance.
Soldering Wetting Process:
Let’s start by outlining the wetting process in detail.
Soldering is the process of fusing two metals using a solder alloy. The two metals are permanently welded together at this permanent junction. Behind the scenes, a wetting process had to have occurred for this process to occur.
The metal material in the solder bonds with the metal on your PCB or in your components during wetting. The solder will melt and adhere to the component, forming the solder link necessary for your process.
The environment needs to meet certain requirements for the wetting process. What you’ll need is as follows:
A spotless copper surface that is uncontaminated.
To the proper temperature.
Different metals respond differently to the wetting process, while others pose a difficulty.
The Wetting Process: Why Is It Important For Soldering?
A proper metal joining form is only when the solder has been properly wetted. The full strength of the solder junction depends on it.
If this doesn’t happen, it might result in several common soldering issues, such as weak junctions that won’t endure. These joints frequently fail the acceptance quality control procedure set up by your business.
Therefore, insufficient wetting in a soldering application could be the main reason for subpar soldering results.
Let’s examine the causes of inadequate solder wetting, though.
Various Elements That May Affect The Wetting Process
Four high-risk elements can frequently hamper the wetting process on a soldering application. These are outlined below:
Oxidized Soldering Cartridge: The wetting capacities of the soldering cartridge you are using are severely limited if it has experienced oxidization. This is so because oxidation creates a barrier that interferes with the wetting process and the easy flow of solder. Utilizing an untinned tip at a too-high temperature frequently results in oxidization.
Insufficient Heating Temperatures: The soldering wetting process suffers from cold and overheated soldering joints. You won’t be able to get the solder to the ideal fluidity level if you underheat it. This hinders the solder from making adequate contact with the component. On the other hand, if the solder level is too high, the wetting process is hampered because the solder burns off quickly as vapor.
Poor Wetting Caused by Insufficient Soldering Technique: The technician’s technique is another factor. The flux is burned or even damaged when too much pressure is applied or when the soldering tip is in contact with the component for an extended period. As was already mentioned, having too little flux or too much heat can seriously impair the wetting process.
Techniques For Avoiding Poor Wetting While Soldering
Simple guidelines can be followed to increase the likelihood of successful solder wetting. They contribute to the creation of a setting that is ideal for facilitating the soldering wetting process.
Environment That Is Clean & Well-Maintained
The wetting process starts to be impeded whenever contaminants, dirt, or moisture are present on your PCB. Before soldering, cleaning the PCB you are working on is always recommended. By doing this, any grime or grease that can affect how solder wets is eliminated. For this, you might use solvent wipes or PCB cleaning products.
Cartridges for Tinned Soldering
Your soldering tips can help avoid oxidation by being tinned. This needs to be incorporated into your practice for cleaning up after soldering. Your hot tips should be soldered before being cleaned, and the station turned off. By doing this, you may extend the shelf life of a soldering cartridge while also improving the wetting process.
High Active Solder Paste
You should always aim to use high-activity solder paste when employing it in your application. This offers a more effective wetting procedure. They assist with wetting in the reflow process as well.
Flux Option
Flux provides a cleansing effect that might lead to better wetting in soldering applications. Surface oxides may be cleared, especially if a higher flux is employed. Also, flux can enhance heat transmission, especially regarding rework applications.
Pcb With Preheated Soldering Iron
You can better activate your flux and avoid oxidation by preheating your PCB. These two advantages will improve wetting in your soldering application. In addition to this, preheating your PCBs has many other benefits because it is a crucial step in PCB assembly.
To Sum Up
We trust that this article has helped clarify the solder-wetting procedure’s significance. Every soldering job needs it.
Your soldering performance will only increase if you know the factors contributing to poor wetting and have some helpful advice for fixing it.
Never forget that it’s not the end of the world if a soldering joint shows signs of poor wetting. You can always fix the joint by allowing it to cool, removing the flux, and starting over from scratch.