How to Choose Super Duplex Steel ER2594 Filler Wire for Your Welding Applications
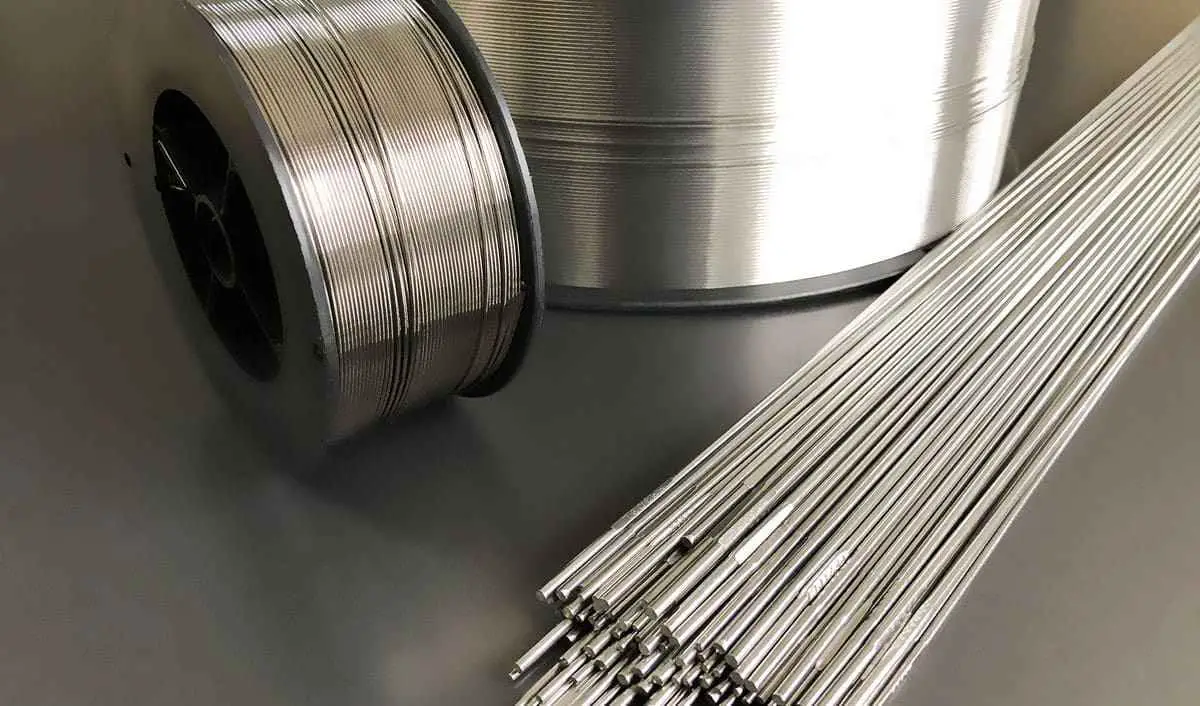
Introduction:
Super Duplex Steel ER2594 Filler Wire is a welding material that is specifically designed to weld super duplex stainless steel, which has high strength and excellent corrosion resistance. ER2594 filler wire is a popular choice for welding applications that require these properties. Selecting the right filler wire is important because it can affect the quality and integrity of the welded joint. The wrong filler wire can lead to poor weld quality, which can compromise the strength and corrosion resistance of the finished product.
Welding is a process of joining two or more pieces of metal together by heating the surfaces to a melting point and adding a filler material to create a strong bond. Welding applications are used in various industries such as construction, manufacturing, and oil and gas. The choice of welding material and process can depend on the type of metal being welded, the desired properties of the finished product, and the environment in which the product will be used.
Properties and Characteristics of Super Duplex Steel ER2594 Filler Wire
Super Duplex Steel ER2594 Filler Wire is a type of welding material that is composed of a blend of metals such as nickel, molybdenum, and chromium. It is specifically designed to weld super duplex stainless steel, which has a high chromium and molybdenum content and offers high strength and excellent corrosion resistance.
Some advantages of using ER2594 filler wire for welding include:
-
High Strength: ER2594 filler wire offers high tensile and yield strength, making it suitable for applications that require high mechanical strength.
-
Corrosion Resistance: ER2594 filler wire provides excellent corrosion resistance, especially in harsh environments such as seawater, acidic or alkaline solutions, and chloride-rich environments.
-
Weld Quality: ER2594 filler wire produces high-quality welds with good impact strength and ductility.
-
Versatility: ER2594 filler wire is suitable for various welding processes, including GTAW, GMAW, and SAW, and can be used in all welding positions.
Some limitations of using ER2594 filler wire include:
When it comes to welding applications that require high strength and corrosion resistance, super duplex steel ER2594 filler wire is a popular choice. Here are some factors to consider when choosing the right ER2594 filler wire for your welding application:
-
Welding Process: Super duplex steel ER2594 filler wire can be used for various welding processes such as Gas Tungsten Arc Welding (GTAW), Gas Metal Arc Welding (GMAW), and Submerged Arc Welding (SAW). Choose the filler wire that is specifically designed for the welding process you will be using.
-
Base Metal: Consider the type of base metal you will be welding. ER2594 is designed to weld super duplex stainless steel (such as UNS S32750 and S32760), so it is important to ensure that the base metal is compatible with the filler wire.
-
Mechanical Properties: Consider the mechanical properties required for the application. ER2594 offers high strength, good ductility, and excellent corrosion resistance, which makes it suitable for various applications such as offshore structures, chemical processing equipment, and seawater desalination plants.
-
Welding Position: Consider the welding position required for the application. ER2594 is suitable for all welding positions, including overhead and vertical positions.
-
Wire Diameter: Choose the appropriate wire diameter based on the thickness of the base metal and the welding position. ER2594 filler wire is available in various diameters ranging from 0.8mm to 2.4mm.
-
Welding Parameters: Follow the manufacturer’s recommended welding parameters for ER2594 filler wire to ensure optimal weld quality.
-
Certification: Choose a filler wire that is certified by relevant standards organizations such as AWS (American Welding Society) or EN (European Norm) to ensure quality and compliance with industry standards.
- Cost: ER2594 filler wire can be more expensive than other types of filler wire due to its high-quality properties and the cost of raw materials.
Overall, when choosing super duplex steel ER2594 filler wire for your welding applications, consider the welding process, base metal, mechanical properties, welding position, wire diameter, welding parameters, and certification to ensure the best results.
Duplex filler wire code refers to a standardized naming convention to identify filler wire materials specifically designed for use in duplex stainless steel welding applications. The code typically includes a letter or a series of letters, numbers, or a combination of both, indicating the specific alloy type, strength, and other essential characteristics such as the level of molybdenum, tungsten, nickel, and nitrogen content of the filler wire. These codes are crucial for selecting the correct filler wire based on the base material, the application, and other factors that impact the quality and durability of the final product. By following the guidelines provided by the welding code, technicians can ensure that they are using the appropriate filler wire and maintain compliance with industry standards and regulations.