What is the Purpose of Wafer Dicing?
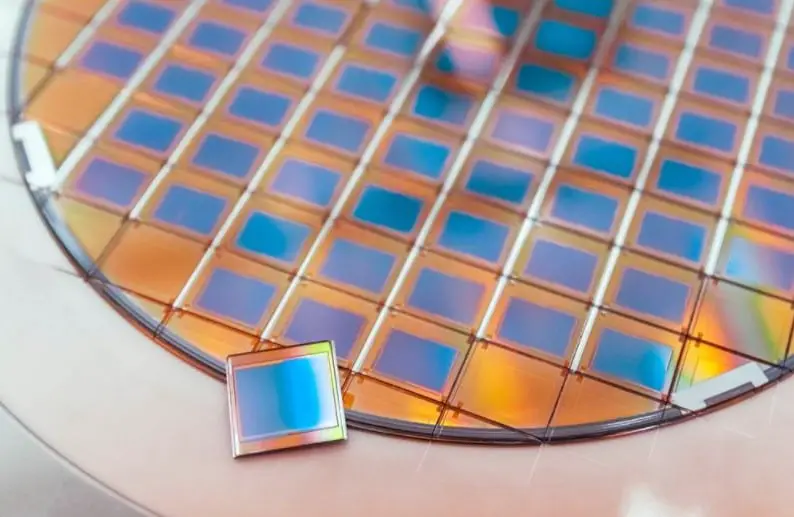
Wafer dicing is the process of separating die (or chips) from semiconductor wafers or other materials into individual dice, which are then packaged in packages or directly placed on circuit boards. This is a very important step in the semiconductor manufacturing process.
The purpose of wafer dicing is to separate individual die from the wafer or other material for use in semiconductor applications such as memory chips, microprocessors, and displays. The process can be done by scribing, laser ablation, or mechanical sawing.
Scribing is a technique that uses only one tool to partially cut through a wafer. Then, a breaking step divides the wafer into individual dice along scribed lines. This process is usually used to singulate chips from silicon wafers, glass, or polymer substrates, as well as for a variety of other applications in the electronics industry.
Whether it’s for a small batch for proof of concept or to accelerate lead times in high-volume production, wafer dicing is a critical process that requires absolute precision. Fortunately, at Platypus Technologies, we offer several customizable services for wafer cutting and dicing of a wide range of substrate materials.
Blade Dicing
For a long time, blade dicing has been the standard method for wafer separation. It’s typically a low cost solution that allows a high degree of control over the dicing process. The key is choosing the proper blade type, which is based on both the material and application requirements.
In addition, a blade’s life is also a factor to consider when deciding on the right blade. For instance, a blade with softer bond material can provide better cut quality and BSC control, but it wears faster than a harder bonded blade. This is especially true of thinner street widths, and the trade off between blade wear and cut quality should be carefully considered when selecting a blade for a given application.
Plasma Dicing
For some MEMS and sensor wafers, plasma dicing is the most suitable technique for releasing the die. This dry, subsurface laser method allows for a safe release of the die without creating particles or liquid contact with the device.
This type of dicing is also popular for micro-electro-mechanical systems (MEMS), which are highly sensitive devices. However, this technique is a relatively slow process that can be challenging for many wafer manufacturers to implement.
Stealth Dicing
For MEMS and sensor wafers, stealth dicing is a more effective option for separating the die because it allows a safer release of the wafer. This type of dicing is usually performed on silicon wafers and can be very fast, but it does require careful passivation design.
The dicing process can be difficult to optimize because it involves precise control over many variables that are affected by the material hardness, brittleness, and thickness of the wafer. As more and more materials, including gallium arsenide (GaAs), lithium tantalite, and copper, enter the market, semiconductor manufacturers must constantly develop ways to improve dicing productivity and enhance cut quality. DISCO’s engineers are continually developing a series of tools that can help manufacturers achieve these goals.