Hydrostatic Weld Testing: A Comprehensive Guide
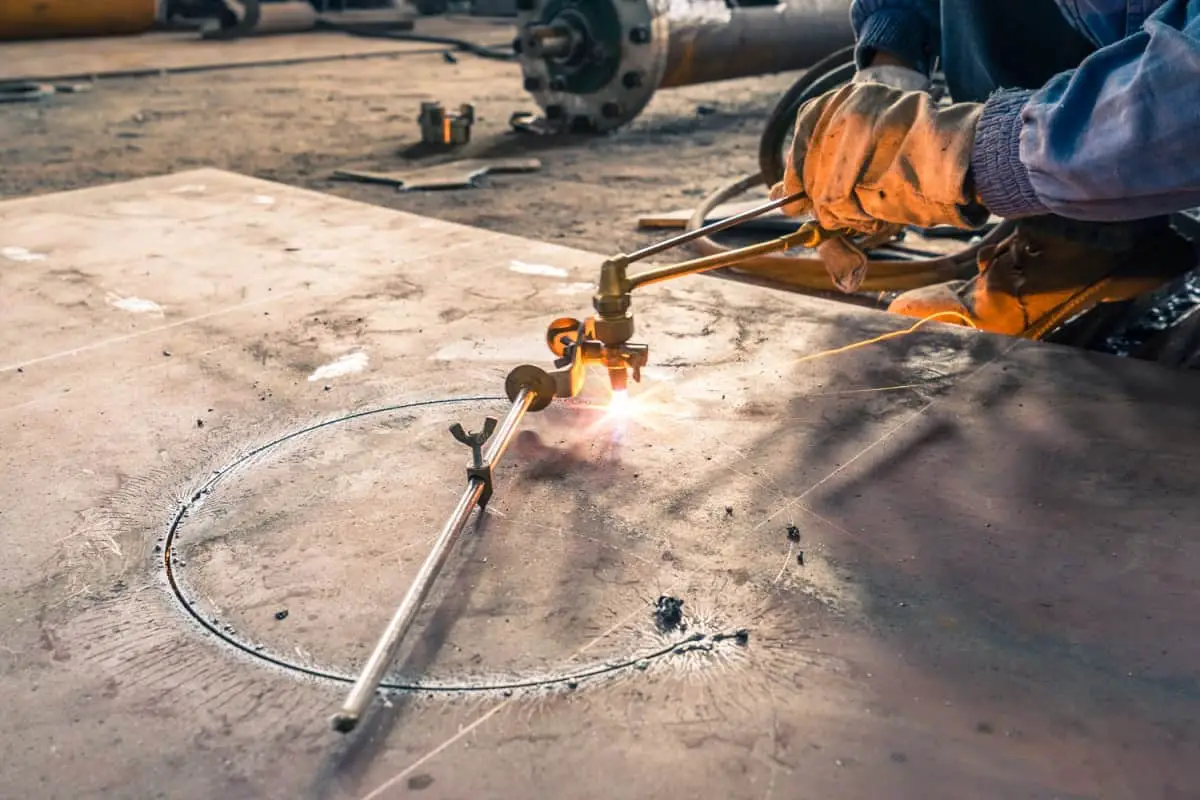
Hydrostatic weld testing is an essential process used in the welding industry to ensure the integrity of welded joints. It involves pressurizing a vessel or pipeline with a liquid to detect any leaks or defects in the welds. In this article, we will explore this in detail, including its purpose, procedure, benefits, and limitations.
What is Hydrostatic Weld Testing?
Hydrostatic weld testing is a non-destructive testing method used to evaluate the strength and integrity of welded joints. In this process, a vessel or pipeline is filled with water or another liquid and pressurized to a predetermined level, usually 1.5 times the maximum allowable working pressure (MAWP) of the vessel or pipeline.
Why is Hydrostatic Weld Testing Important?
It is important because it ensures that welded joints can withstand the pressure and stress of normal operations. This testing method can detect leaks, cracks, and other defects in welds that could lead to equipment failure or safety hazards. By detecting and repairing these defects early, it can prevent accidents, reduce downtime, and save money.
Preparation for Hydrostatic Weld Testing
Before performing a hydrostatic weld test, it is essential to prepare the vessel or pipeline properly. The preparation process includes:
- Cleaning the inside of the vessel or pipeline to remove any debris or contaminants that could affect the test results.
- Sealing all openings in the vessel or pipeline to prevent any leaks during the test.
- Installing pressure gauges and relief valves to monitor and control the pressure during the test.
Procedure for Hydrostatic Weld Testing
The procedure for this involves the following steps:
- Filling the vessel or pipeline with water or another liquid.
- Pressurizing the vessel or pipeline to the desired level, usually 1.5 times the MAWP.
- Holding the pressure for a predetermined time, usually between 10 and 30 minutes.
- Inspecting the vessel or pipeline for any leaks, cracks, or other defects.
- Releasing the pressure and draining the liquid from the vessel or pipeline.
Interpretation of Hydrostatic Test Results
The results of a hydrostatic weld test are interpreted by inspecting the vessel or pipeline for any leaks, cracks, or other defects. If no defects are found, the weld is considered to be sound. If defects are detected, further examination and repair may be required before the vessel or pipeline can be put into service.
Benefits of Hydrostatic Weld Testing
Hydrostatic weld testing offers several benefits, including:
- Detecting defects early before they lead to equipment failure or safety hazards.
- Providing a quantitative measure of the strength and integrity of welded joints.
- Ensuring compliance with industry standards and regulations.
Limitations of Hydrostatic Weld Testing
Although it is a reliable method for detecting defects in welded joints, it does have some limitations, including:
- The test can only detect defects that are open to the surface of the weld. It cannot detect defects that are hidden beneath the surface.
- The test is time-consuming and can be expensive, especially for large vessels or pipelines.
- The test can only be performed on vessels or pipelines that can safely contain the test pressure.
Safety Precautions during Hydrostatic Weld Testing
It involves pressurizing vessels or pipelines, which can be hazardous if proper safety precautions are not taken. Some of the safety precautions that should be followed during hydrostatic weld testing include:
- Wearing appropriate personal protective equipment, including eye protection and gloves.
- Ensuring that all pressure gauges and relief valves are properly installed and functioning.
- Venting all air from the vessel or pipeline before filling it with liquid.
- Performing the test in a controlled environment with proper ventilation.
Common Myths and Misconceptions about Hydrostatic Weld Testing
There are several myths and misconceptions about it, including:
- Myth: Hydrostatic testing is destructive.
- Fact: Hydrostatic testing is a non-destructive testing method that does not damage the vessel or pipeline being tested.
- Myth: Hydrostatic testing can detect all types of defects in welded joints.
- Fact: Hydrostatic testing can only detect defects that are open to the surface of the weld. It cannot detect defects that are hidden beneath the surface.
- Myth: Hydrostatic testing is not required for new vessels or pipelines.
- Fact: Hydrostatic testing is often required by industry standards and regulations for new vessels or pipelines.
Hydrostatic Weld Testing vs. Radiographic Testing
Radiographic testing is another non-destructive testing method used in the welding industry to detect defects in welded joints. Unlike hydrostatic testing, radiographic testing uses X-rays or gamma rays to inspect the internal structure of the weld. While both methods have their advantages and disadvantages, hydrostatic testing is typically less expensive and easier to perform than radiographic testing.
Hydrostatic Weld Testing vs. Pneumatic Testing
Pneumatic testing is another non-destructive testing method like isolations and hydrotesting that involves pressurizing vessels or pipelines with air instead of liquid. While both methods are effective for detecting defects in welded joints, pneumatic testing is generally more hazardous than hydrostatic testing because compressed air can cause explosions or other safety hazards.
Conclusion
Hydrostatic weld testing is a critical process in the welding industry that helps ensure the safety and integrity of welded joints. By detecting defects early and preventing equipment failure and safety hazards, it can save money and protect lives. However, it is essential to follow proper safety precautions and to understand the limitations of this testing method to achieve the best results.