The Benefits of Using Copper Tungsten Electrodes in High-Current EDM Applications
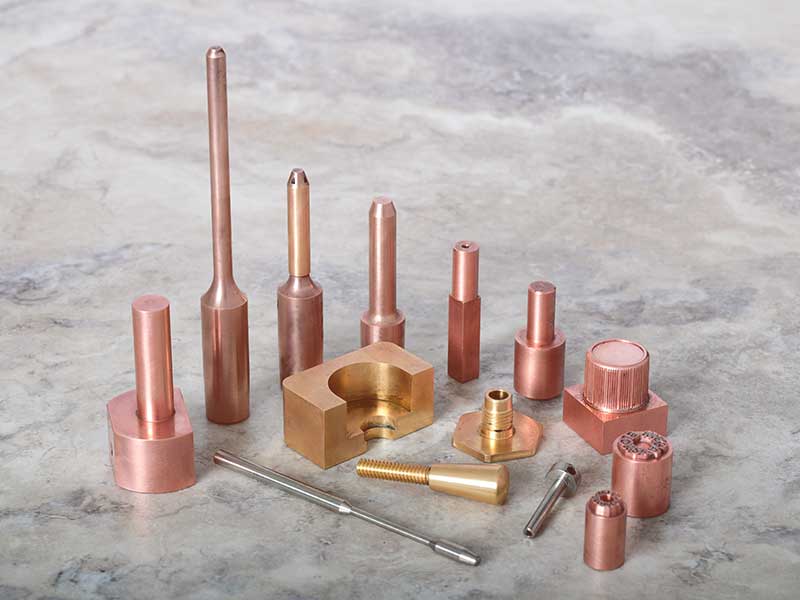
Copper tungsten electrodes are a type of electrode material used in electrical discharge machining (EDM), a manufacturing process that uses sparks of electricity to remove material from a workpiece. Bonding copper makes copper tungsten electrodes to tungsten, a dense and highly heat-resistant metal. The combination of these materials provides several benefits for EDM applications.
Copper Tungsten Electrodes are known for their high electrical conductivity, making them ideal for high-current EDM applications. They also have a high thermal conductivity, which helps to dissipate heat generated during the EDM process and prolong the life of the electrode. Copper tungsten electrodes are also resistant to erosion and wear, making them ideal for EDM applications that involve hard machining materials such as carbides, ceramics, and superalloys.
Properties of copper tungsten electrodes
Copper tungsten electrodes are a type of electrode material used in electrical discharge machining (EDM) and are known for their unique properties. Some of the most important properties of copper tungsten electrodes include the following:
- High electrical conductivity: Copper tungsten electrodes have a high electrical conductivity, which makes them ideal for use in high-current EDM applications.
- High thermal conductivity: Copper tungsten electrodes have a high thermal conductivity, which helps to dissipate heat generated during the EDM process and prolong the life of the electrode.
- Resistance to erosion and wear: Copper tungsten electrodes are resistant to deterioration and wear, making them ideal for EDM applications that involve hard machining materials such as carbides, ceramics, and superalloys.
- High density: Tungsten, the primary component of copper tungsten electrodes, is a dense metal that contributes to the overall high thickness of the electrode. This high density helps improve the EDM process’s stability and accuracy.
- Good arc stability: Copper tungsten electrodes provide good arc stability, which helps to ensure consistent results in the EDM process.
These properties make copper tungsten electrodes a versatile and reliable option for EDM applications, particularly in high-current and high-heat applications where the durability and stability of the electrode are essential.
The Versatility and Durability of Copper Tungsten Electrodes for EDM Applications
These electrodes offer several benefits that make them a popular choice in EDM applications, including:
- Versatility: Copper tungsten electrodes can be used in a variety of EDM applications, including high-speed machining, precision machining, and drilling. They are suitable for many materials, including carbides, ceramics, superalloys, and other hard-to-machine materials.
- Durability: Copper tungsten electrodes are highly resistant to erosion and wear, which helps to extend their life and maintain their accuracy and precision. It can result in reduced maintenance and replacement costs and improved production efficiency.
- High Electrical Conductivity: Copper tungsten electrodes have high electrical conductivity, allowing for efficient electrical energy transfer to the workpiece. This results in improved machining results and reduced energy consumption.
- High Thermal Conductivity: Copper tungsten electrodes have a high thermal conductivity, which helps to dissipate heat generated during the EDM process. This prolongs the electrode’s life and helps maintain a consistent machining performance.
In conclusion, copper tungsten electrodes are a versatile and durable choice for EDM applications due to their high electrical conductivity, thermal conductivity, and resistance to erosion and wear. These properties make them an excellent choice for manufacturers looking to improve the efficiency and performance of their EDM processes.