3 Easy Ways to Make Screen Printing Faster
Screen printing is a versatile and widely-used method for transferring designs onto various surfaces, from clothing to signage and more. However, the process ...
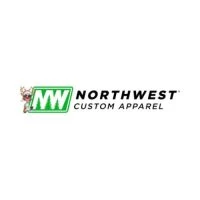
Screen printing is a versatile and widely-used method for transferring designs onto various surfaces, from clothing to signage and more. However, the process ...